Rispetto ai precedenti convegni sulla manifattura digitale, il clima è cambiato. Lo conferma in apertura del convegno di presentazione dell’Osservatorio Industria 4.0 del Politecnico di Milano, Massimo Dal Checco, Presidente del Gruppo ICT e Servizi alle Imprese di Assolombarda, portando a riprova il balzo degli ordinativi: +22% nel 2017, rispetto allo stesso periodo 2016, trimestre su trimestre. Al tempo stesso, Dal Checco auspica che la crescita non sia generata solo dagli incentivi del piano Industria 4.0, ma soprattutto dalla comprensione da parte delle imprese della necessità di innovare per competere.
Who's Who
Massimo Dal Checco
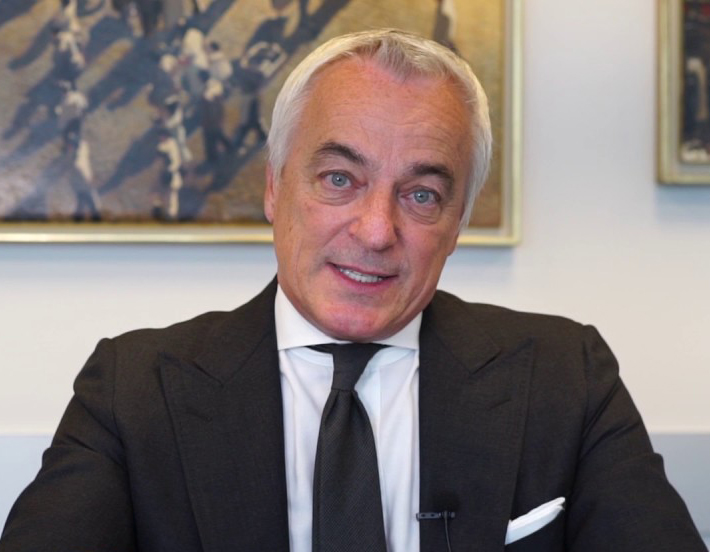
Analoga preoccupazione viene espressa da Marco Taisch, Responsabile Scientifico dell’Osservatorio Industria 4.0 della School of Management del Politecnico di Milano: “Un anno fa, quando siamo partiti con l’Osservatorio Smart Manufacturing, il 38% non sapeva nemmeno cosa fosse la rivoluzione Industria 4.0, mentre oggi, come l’indagine degli Osservatori rileva, solo l’8% lo ignora” (figura 1).
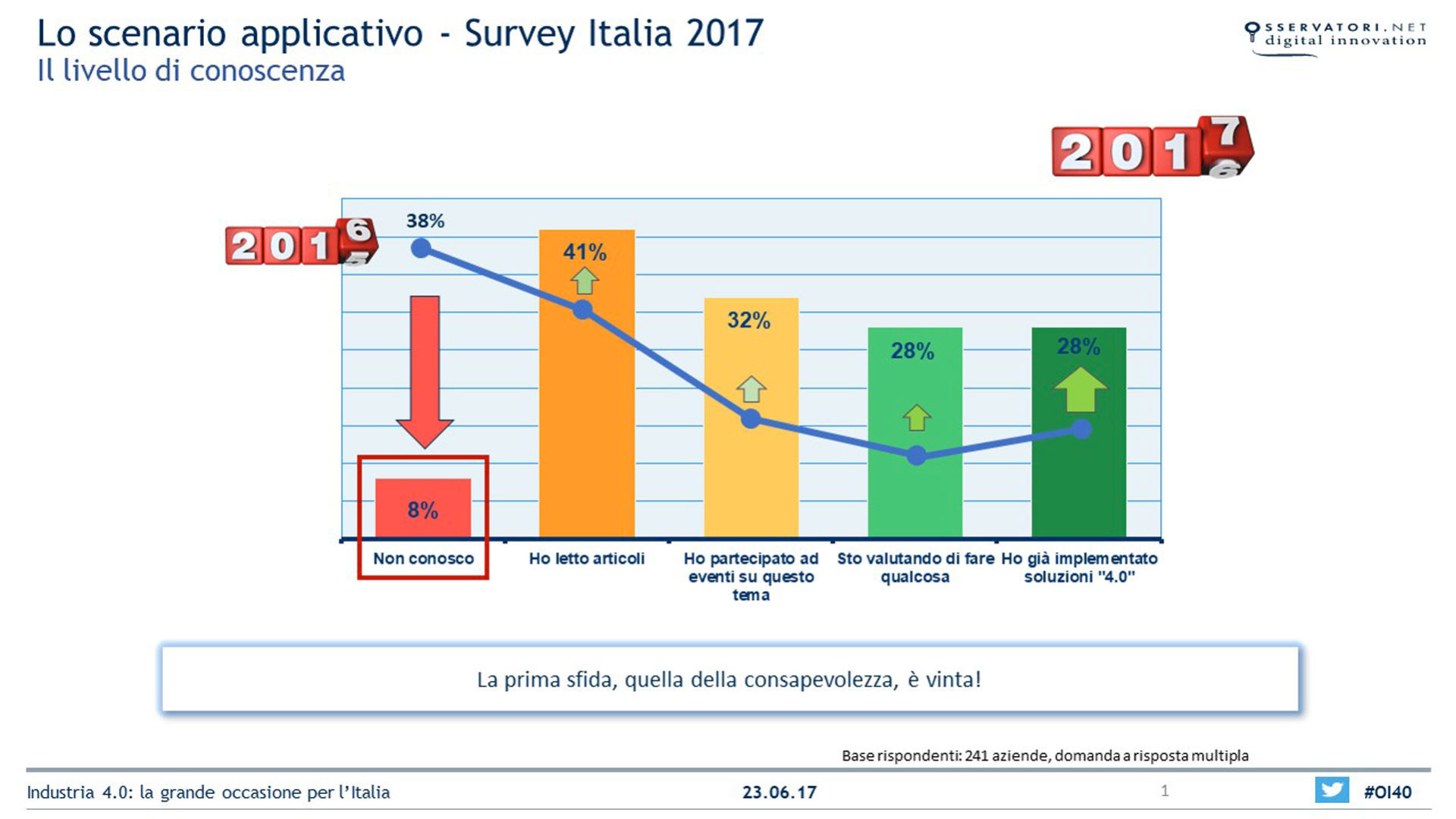
“Su questo tema, l’Italia si sta giocando il suo futuro industriale – aggiunge Taisch – Serve la consapevolezza che Industry 4.0 non è solo una rivoluzione tecnologica e che avrà un impatto significativo su lavoro, competenze specifiche, società…”. Necessario dunque evitare un’ondata di investimenti spinta più dall’opportunità fiscale che da una vera consapevolezza delle potenzialità della Quarta Rivoluzione Industriale per la competitività delle imprese e del sistema industriale italiano. Un potenziale che, secondo la definizione di Giovanni Miragliotta, Direttore dell’Osservatorio Industria 4.0 deriva soprattutto dalla maggiore interconnessione delle risorse delle imprese (impianti, persone, informazioni), sia interne alla fabbrica sia distribuite lungo la catena del valore.
Who's Who
Marco Taisch
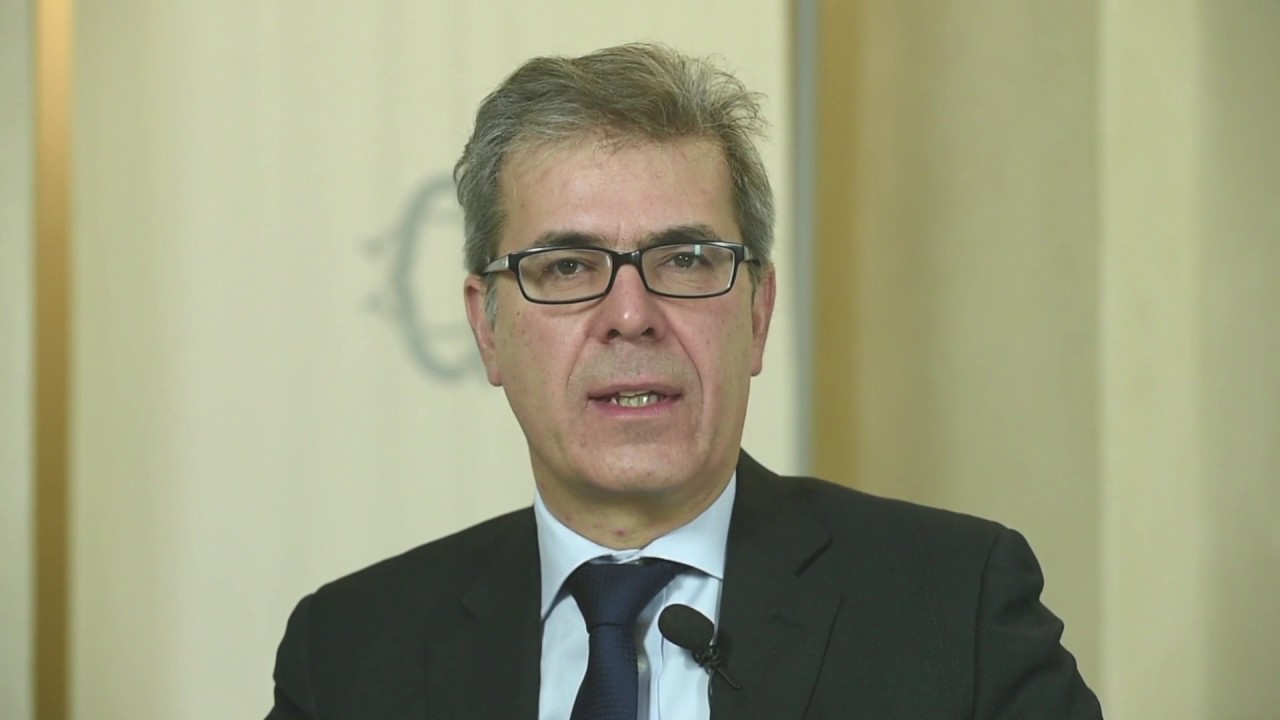
Anche Roberto Zuffada, Head of Digital Enterprise Team di Siemens manifesta, nel corso di una delle tavole rotonde che si sono svolte durante il convegno, qualche preoccupazione, pur ammettendo che la focalizzazione sulla tecnologia faccia ben sperare di poter prendere il treno della digitalizzazione per aumentare la flessibilità del sistema industriale: “Ma per centrare l’obiettivo serve un piano completo di digitalizzazione dell’azienda, che non è automatico: l’IT spesso non è ancora vista come una componente strategica negli ambiti produttivi”.
I successi di Indutria 4.0
Ma nonostante i timori, Industria 4.0 viaggia a gonfie vele. L’indagine ha registrato, per esempio, interessanti progressi nel numero di applicazioni (800) riconducibili a Industria 4.0, con una media di 3,4 per azienda: “Tuttavia il progresso è concentrazione in poche aziende: il 30% delle quali utilizza il 60% delle applicazioni”, commenta Miragliotta. Il 30% delle aziende ha infatti adottato almeno 3 applicazioni in più rispetto allo scorso anno, mentre il 50% delle aziende non si è mosso. Ma chi ha progredito ne ha tratto vantaggio: ”Industria 4.0 sta diventando un differenziale competitivo”, sottolinea Miragliotta.
L’indagine ha infatti correlato il livello di attività in campo 4.0 con indicatori di crescita e produttività. Dall’analisi dell’Osservatorio, emerge che le imprese che si sono più distinte nell’adozione hanno beneficiato di un incremento di produttività del capitale investito, grazie alla capacità di meglio sfruttare le risorse e far interagire persone, macchinari e patrimonio informativo. Si è rilevato sia un aumento di fatturato dell’8% (fatto 100 quello del 2010), sia, particolarmente significativo, di redditività (figura 2).
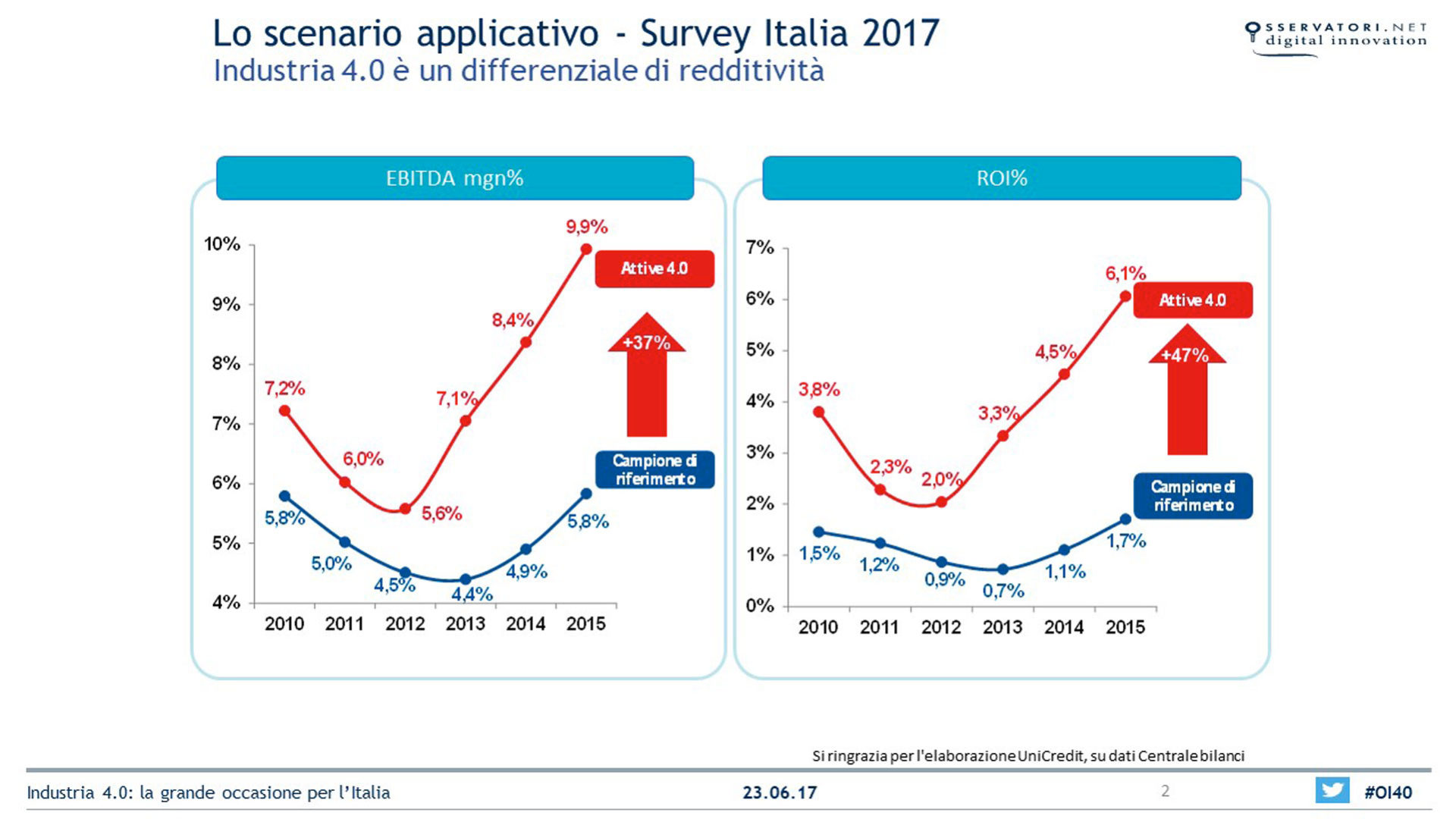
È indubbiamente aumentata la consapevolezza e con essa, di pari passo, il mercato, che ha raggiunto 1,6-1,7 miliardi di euro, in crescita del 25% rispetto allo scorso anno; il confronto è stato fatto a parità di perimetro, prendendo in considerazione solo le 3 aree analizzate anche lo scorso anno invece delle 5 di quest’anno che hanno visto l’introduzione di Advanced automation e HMI (interfaccia uomo-macchina), che assorbono una quota ancora modesta, ma riscuotono grande interesse (figura 3).
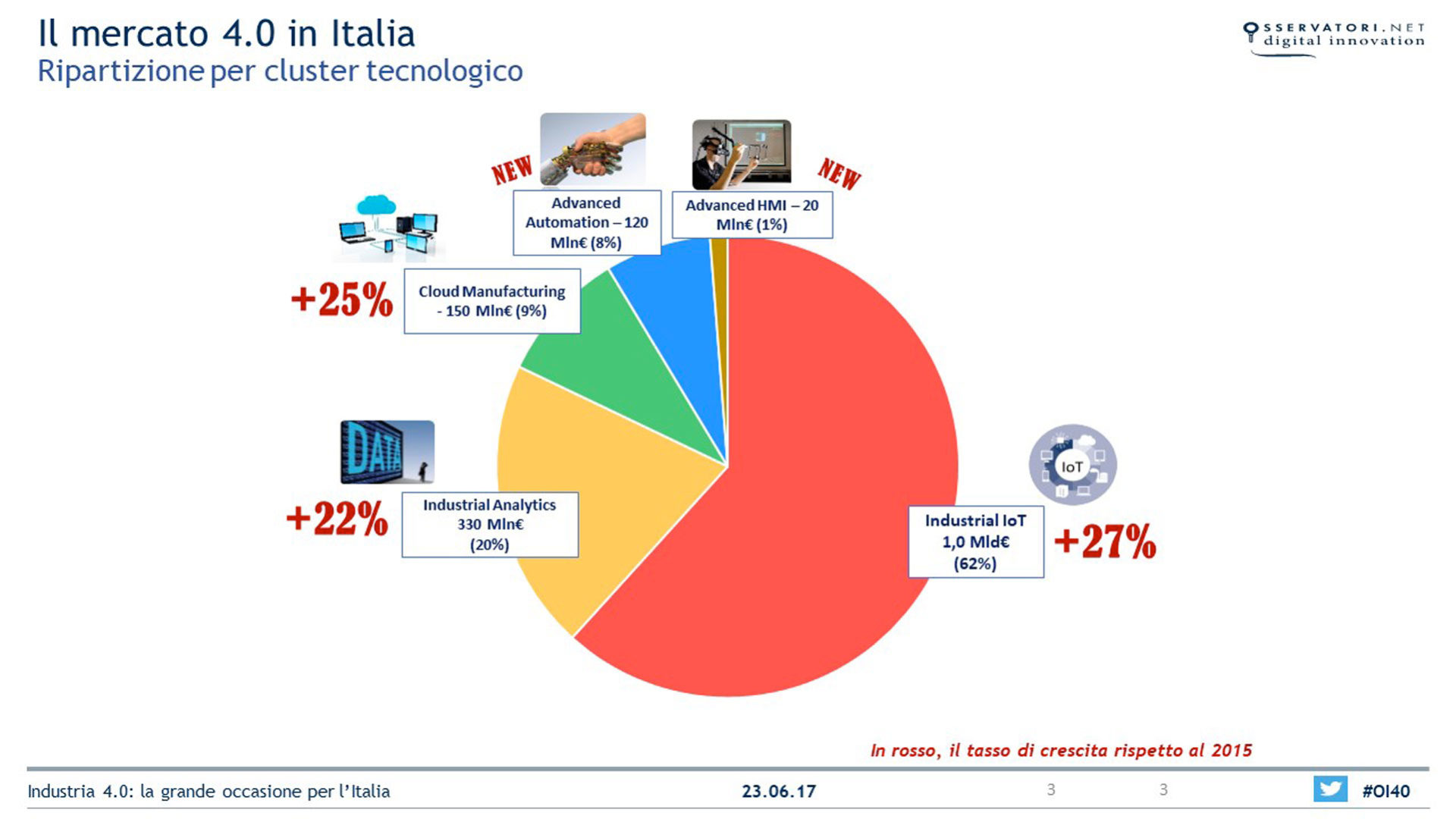
“Il fatto che la quota di export si sia ridotta solo a livello percentuale al 16% (il dato 2015 era 20%), in un quadro generale di crescita del mercato è il segno dell’aumento di domanda interna – dice Miragliotta che aggiunge – Questo scenario chiama anche le imprese dell’offerta a una grande responsabilità, visto che dovranno consigliare ai propri clienti quello che effettivamente serve loro e in che misura”.
“Ci vorrebbe più chiarezza dal lato dell’offerta, per aiutare davvero le aziende a crescere non fornendo soluzioni tradizionali travestite da 4.0”, ammette in una delle tavole rotonde, Fabio Massimo Marchetti, Business Development, Sales & Marketing Var Sirio Industria – Var Group, facendo riferimento a soluzioni informatiche di fatto tradizionali alle quali ci si limita a cambiare il nome dopo un approssimativo maquillage.
Che fare? I primi tre passi del percorso di trasformazione
Miragliotta suggerisce un percorso di trasformazione in tre passi (verifica della readiness, sperimentazione, mastering) che tenga conto di alcune criticità mutuate anche dalla storia passata: “Il primo passo è la digital readiness [la capacità di interagire efficacemente con piattaforme, soluzioni e servizi a base digitale – ndr] senza la quale non è possibile intraprendere il percorso. Segue la sperimentazione, che è quanto stanno facendo le imprese italiane in modo confrontabile con l’estero in ambiti analoghi”. A questo punto però il rischio è la commoditizzazione dei processi come è accaduto, per esempio, con l’introduzione degli ERP: “Tutti hanno migliorato, ma si è ridotto il gap fra le imprese migliori e peggiori – spiega Miragliotta – Se accadesse lo stesso nel manifatturiero si perderebbero specificità e fattore competitivo delle singole imprese”. Per evitare questo rischio, il passo successivo è il mastering, che consiste nel comprendere in profondità le tecnologie senza accontentarsi di una lettura di primo livello; credere nei dati; ridisegnare cultura e competenza delle imprese; rimescolare capacità di innovazione, continuità e disruption.
Who's Who
Giovanni Miragliotta
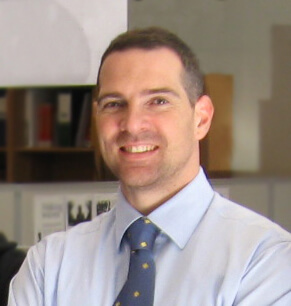
Capire le tecnologie significa comprendere le tendenze. “In analogia con quanto è accaduto con gli smart phone con l’introduzione dei sistemi operativi che hanno disaccoppiato hardware e applicazioni, al device di fabbrica dotato di sistema operativo si applicano tutte le architetture cloud immaginate per i computer”, spiega Miragliotta.
Credere nei dati (effettuando gli opportuni interventi di unificazione dei database a prescindere dalla provenienza) significa poter misurare i risultati in modo omogeneo. È questa la condizione per il miglioramento, che comporta il ridisegno delle competenze e delle culture.
Il tema delle competenze viene sottolineato, sempre nel corso delle tavole rotonde, anche da Giampaolo Codelupi partner Key2people Executive Search: “Non servono solo nuove competenze sulle tecnologie digitali, ma anche di processo e business. Va cambiato il mindset delle persone, il loro approccio all’innovazione, la capacità di apertura e flessibilità, quella di fallire e imparare”.
Anche Giancarlo Oriani, CEO di Staufen Italia insiste sulle competenze. Da un’indagine commissionata dall’azienda su 120 imprese, risulta che, rispetto al 2015, le aziende che hanno progetti di digitalizzazione sono raddoppiate e che il 78% prevede di avere successo grazie a 4.0, ma molte ritengono di aver fatto poco e di avere un gap di competenze che riguarda soprattutto i manager. “Difficile che un manager possa definire una road map valida se non conosce approfonditamente ciò di cui sta parlando”, sottolinea.
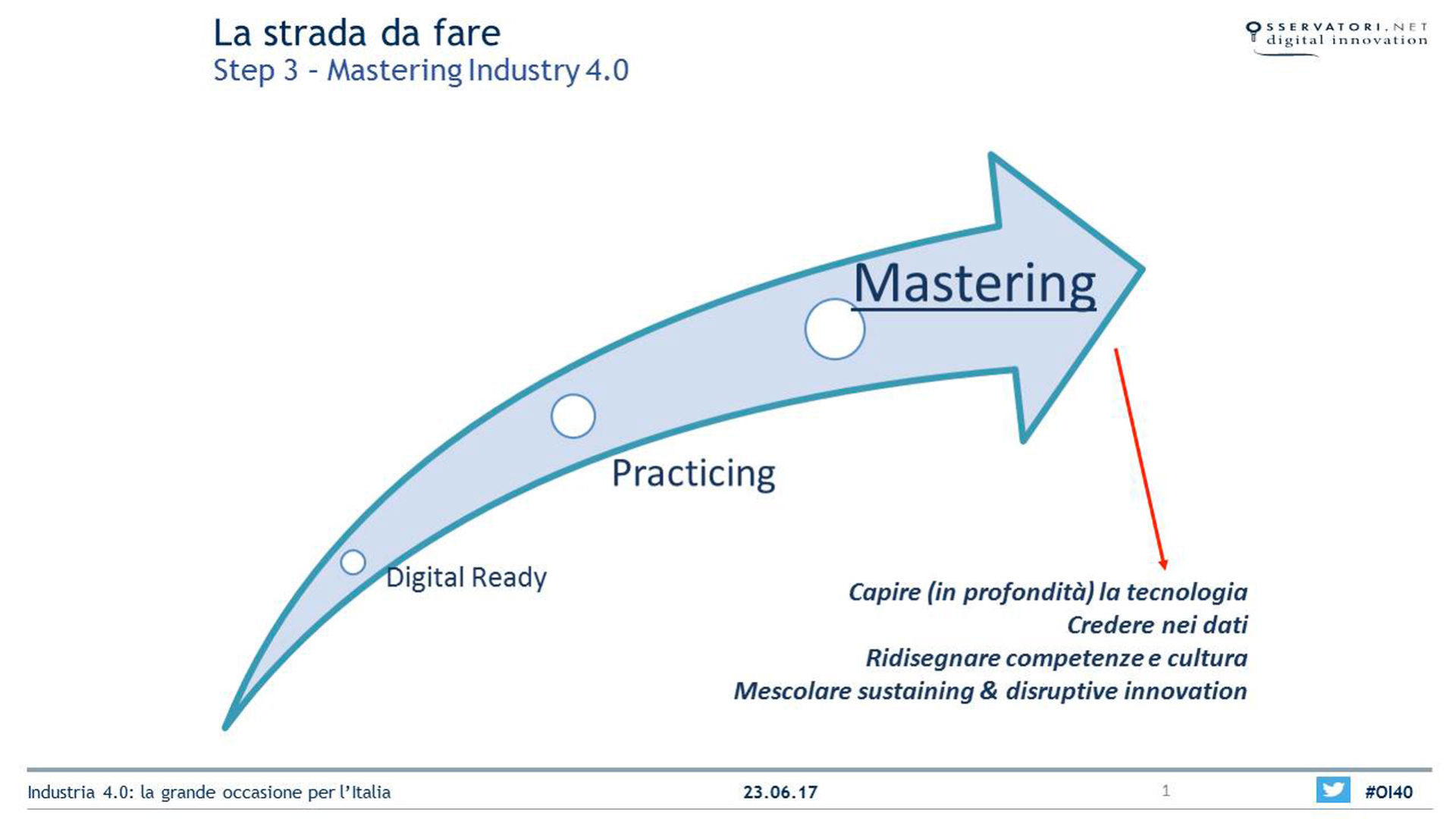
Per l’attuazione del modello 4.0, conclude Miragliotta, serve bilanciamento fra disruptive (più rischi, lungo termine, vantaggi elevati) e sustaining (pochi rischi, tempi brevi, limitati vantaggi) (figura 4) e conclude con un messaggio di ottimismo: “La prima sfida è vinta! Le imprese italiane sono finalmente consapevoli della centralità di Industria 4.0 e si sta facendo un grande lavoro di squadra, anche grazie al Piano Nazionale Industria 4.0, che ancora non ha messo a terra tutto il suo potenziale, ma ha già contribuito ad un incremento del 25% del mercato nel 2016 rispetto al 2015”.