In un anonimo capannone sparso nella zona industriale a nord di Piacenza si trova una delle strutture di eccellenza per lo sviluppo del settore manifatturiero italiano, il Centro Tecnologico Applicativo della Siemens (vedi box). Ed è in questo ambiente, a metà tra una scuola e una smart factory, che in concomitanza con l’edizione 2017 della SPS IPC Drives Italia, la più importante fiera italiana dell’automazione industriale che si tiene ogni anno a Parma, si è svolto il consueto incontro con la stampa di settore per illustrare la posizione e gli obiettivi della società.
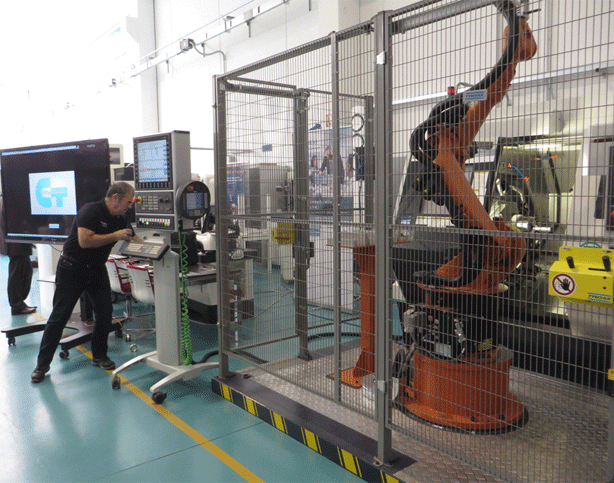
Un angolo del centro Tecnologico applicativo di Piacenza; sulla destra una stazione robotizzata.
Giuliano Busetto, responsabile dell’area che in Italia raggruppa le divisioni Digital Factory e Process Industries & Drives (DF e PD), ha esordito con una breve esposizione dei risultati dello scorso esercizio. Che si possono così sintetizzare: una crescita del 6% rispetto al 2015 del fatturato totale, che ha raggiunto i 79,64 miliardi di euro, e una crescita significativa degli investimenti per la ricerca e sviluppo, che negli ultimi anni sono passati dai 4 miliardi del 2014 a 5 stimati per l’anno in corso, con un aumento del 25%. Importante nella strategia Siemens è l’apporto delle divisioni DF e PD a livello globale. La prima, che contribuisce al 13% del fatturato totale, è la terza realtà nel mondo nel settore se si considera l’insieme dell’offerta ma è leader globale nel sottosettore chiave della Factory Automation (non c’è smart factory se prima non si automatizza l’impianto). Quanto alla seconda, il cui apporto al fatturato è dell’11%, è nel mondo ‘solo’ quinta, ma è quella nella quale oggi Siemens punta di più. Infatti per equilibrare il peso della digitalizzazione nel mondo fisico della fabbrica con quello dei processi nel mondo virtuale, negli ultimi dieci anni sono state fatte molte acquisizioni di software house. Ultima in ordine di tempo, e tra le più ricche, quella di Mentor Graphics, acquisita nel novembre scorso per 4,5 miliardi di euro ‘cash’ e dall’aprile di quest’anno parte di Siemens Plm.
Smart factory, il ruolo delle risorse umane
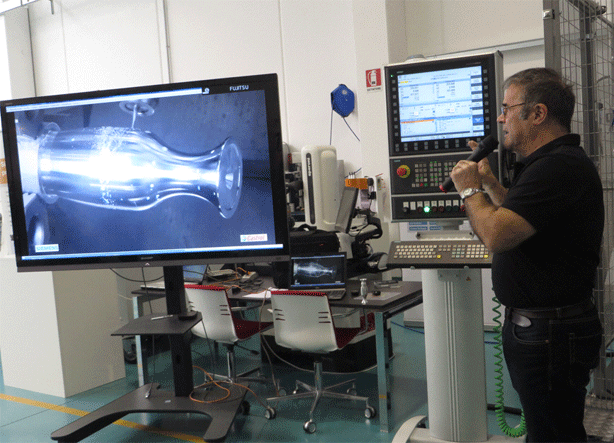
Dimostrazione su grande schermo di machine automation cycle.
In Italia, dove il fatturato totale 2016 è stato di oltre 1,90 miliardi, con una crescita del 7%, più alta quindi della media rispetto all’anno prima, entrambe le divisioni, Digital Factory e Process Industries & Drives, sono costantemente cresciute nel tempo al tasso medio del 6% annuo, sia in volumi che in quote di mercato. Data la sede dell’incontro, che è di fatto un centro di formazione, Busetto ha dato particolare rilievo al potenziamento delle risorse umane. Tra il 2015 e il 2016 sono state assunte un centinaio di persone, per il 60% circa giovani di meno di trent’anni, in maggioranza destinati all’area commerciale e di customer service, a supporto appunto della crescente penetrazione del mercato, ma con una buona quota di figure tecniche e di specialisti. Parte di queste nuove risorse, oltre ovviamente ad altre già presenti, sono organizzate in un Digital Enterprise Team strutturato su gruppi a base regionale che fanno capo a un quartier generale nazionale e interagiscono con le business unit DF, PD e SISW (Siemens Software). Lo scopo è di diventare “gli specialisti per definizione” della Digital Enterprise, aiutando le imprese utenti nello svilupparne i temi e lavorando con le BU e la forza vendita nel trovare i clienti e le user case più promettenti.
Ovviamente, alle risorse umane, per quanto motivate e preparate, occorre dare anche la tecnologia. Su questa, la linea Siemens è chiara. Come ha detto Busetto: “L’incontro e il collegamento tra la produzione reale e quella virtuale è dato dal ‘digital twin’, la copia che duplica proprietà, caratteristiche e prestazioni non solo del prodotto fisico, ma anche del processo produttivo e dell’intera fabbrica”.
Ecco la strategia Siemens: dal ‘braccio’ alla ‘mente’
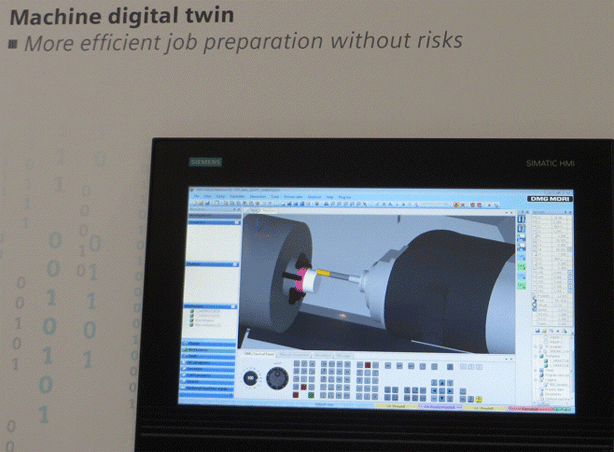
Pannello dimostrativo del gemello digitale di un tornio (in funzione) e del relativo quadro di controllo.
In effetti, più che sul gemello del prodotto è proprio su quello del processo e dell’impianto che insiste la società. Forte del primato nella factory automation propone un approccio alla digital enterprise che parte dal “braccio” esecutivo del Mes (manufacturing execution system, che da parte sua già si va estendendo all’additive manufacturing) per arrivare alla sua totale integrazione con il Plm e gli altri componenti della “fabbrica intelligente”: la gestione del magazzino e delle scorte; l’interconnessione con i sistemi dei subfornitori e dei partner; lo scambio biunivoco di dati e informazioni dal produttore all’utente finale; la sicurezza fisica e logica e altre ancora delle nove tecnologie che Siemens considera abilitanti per la nuova impresa. Strumento principale di questo percorso è naturalmente MindSphere, la piattaforma di sviluppo per l’IoT (che per politica aziendale Siemens chiama ‘sistema operativo’) fruibile su cloud Sap, AtoS, Microsoft Azure o su cloud privato. MindSphere, ricorda Busetto: “consente con MindConnect di acquisire e aggregare dati forniti da macchine e impianti, sia nostri sia di terze parti, anche fisicamente lontani, garantendo una comunicazione sicura, oltre a fornire applicazioni (le MindApps – ndr) di tipo analitico per analizzarne il comportamento e anticiparne i problemi o specifiche per realizzare nuovi servizi digitali”.
Un centro per promuovere l’IndustrIA 4.0 in ItaliaLa creazione, nel 2011, del Centro Tecnologico Applicativo (in sigla TAC, all’inglese) fa parte del contributo di Siemens Italia allo sviluppo dell’industria manifatturiera nazionale. In una superficie di circa 700 mq, il TAC di Piacenza riunisce tre funzioni: centro per la dimostrazione pratica sull’impiego della piattaforma Siemens Sinumerik; ‘smart factory’ sperimentale attrezzata per dimostrare le sinergie tra automazione e software Plm; centro di formazione d’alto livello con proprie stazioni di simulazione Sinumerik e software di programmazione Siemens Sinutrain. Lo scopo è mettere a disposizione di produttori, costruttori di macchinari ed istituti superiori e universitari corsi d’istruzione e formazione avanzata sui moderni sistemi di controllo numerico per macchine utensili e robot industriali. In quest’ottica il TAC collabora con il Politecnico di Milano, il Politecnico di Torino , il Centro Salesiano per la formazione e aggiornamento professionale e diversi altri istituti tecnici e scuole professionali. |