Durante questa pandemia si stanno evidenziando i benefici derivanti dagli investimenti pregressi in ambito Industria 4.0 e nella digitalizzazione dei processi. Quali tecnologie e quali trasformazioni organizzative saranno mantenute e risulteranno indispensabili per il new normal? Ne hanno discusso i partecipanti a una delle tavole rotonde virtuali, all’interno del convegno Digital new normal: essere 4.0 ai tempi del Covid, organizzato dall’Osservatorio industria 4.0 del Politecnico di Milano.
Gli investimenti in tecnologia digitale hanno garantito e stanno garantendo continuità industriale anche in presenza dell’emergenza Covid. Concorda con questa affermazione Giacomo Salina, presidente Castel Italia, che da fine 2017 ha realizzato un primo investimento per raccolta dati in real time su 3 linee pilota e oggi ha esteso l’interfacciamento tramite grandi monitor touch a tutte le principali linee produttive con l’obiettivo di semplificare, razionalizzare e rendere più amichevole il dialogo uomo-macchina.
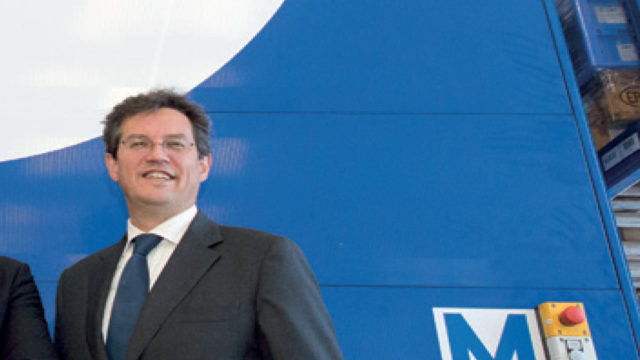
Gradualmente la documentazione per le diverse aree è passata da formato cartaceo a formato elettronico, con la raccolta dati di produzione real time. “Il Covid ha sancito in maniera netta un cambio di abitudini – sottolinea – Oggi godiamo dei benefici degli investimenti pregressi in Industria 4.0: grazie all’adozione di piattaforme IoT in produzione per la raccolta dati, lavoriamo in sicurezza garantendo il distanziamento fra le persone senza perdita di informazioni”.
Gianni Dal Pozzo, CEO Considi, come osservatore esterno di modelli di fabbrica, sostiene: “Le aziende che hanno implementato tecnologie per la digitalizzazione del processo hanno avuto una sorta di vantaggio competitivo, un’accelerazione verso una nuova normalità in termini di produttività e efficienza”. Queste riflessioni derivano da quanto evidenziato da un osservatorio realizzato in periodo Covid, pensando alla ripartenza, con il quale sono stati intervistati 40 imprenditori rappresentativi di diversi settori industriali e differenti esperienze (dalla chiusura totale al raddoppio della produzione).
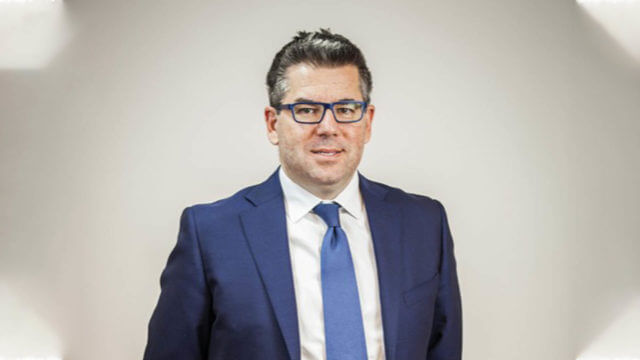
La gestione in remoto degli asset e l’integrazione It-Ot, caratteristica chiave dei processi Industria 4.0, ha svolto un ruolo fondamentale in epoca Covid per garantire la continuità operativa, conferma Pier Paolo Parabiaghi, Sales Manager Robotics e responsabile per la divisione IIOT di Fanuc Italia: “Fra le nostre aziende clienti, quelle che hanno abilitato le produzioni adottando industrial IoT, sono riuscite a sfruttare la possibilità di amministrare da remoto senza un presidio in locale. I più evoluti si stanno avvicinando al nostro sistema industrial IoT completo, sviluppato in collaborazione Cisco”. Il sistema permette la raccolta dei dati dalle macchine di produzione (parte OT) per elaborarli al fine di predictive o preventive maintenance, mettendo i dati a disposizione delle diverse BU.
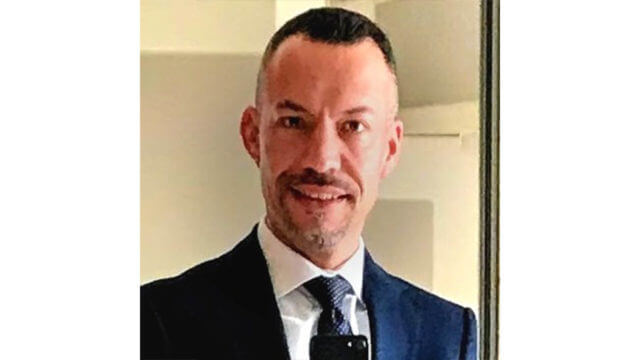
La pandemia che ha certamente portato grandi difficoltà può essere vista anche come occasione per rinnovare i processi aumentando la digitalizzazione e il livello di smart working in determinate aree di operation. Ne è convinto Giovanni Bottinelli, Technologies & Quality Director di Italcementi, che porta ad esempio il caso dei prelievi dei campioni di cemento per la mercatura CE senza la presenza dell’ispettore dell’ente di controllo all’interno del sito.
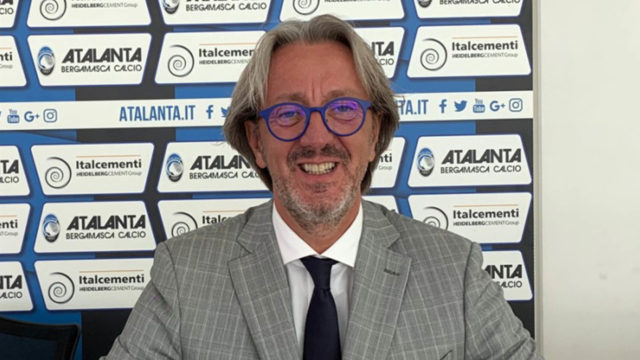
Un’attività non marginale se si considera che Italcementi dispone di 15 stabilimenti per la produzione di cemento e 110 impianti per la produzione di calcestruzzo con un numero di oltre 500 visite l’anno di personale degli enti di certificazione. Le ispezioni erano necessarie anche durante il lockdown, visto che alcuni impianti hanno continuato a produrre perché l’attività era finalizzata alla realizzazione di importanti opere (es. ponte Genova) o realizzazione di manufatti per opere sanitarie di emergenza. “La verifica documentale poteva avvenire attraverso una piattaforma, mentre il prelievo campioni e la verifica di conformità non avrebbe potuto essere eseguita, senza il soccorso di un’applicazione di messaggistica istantanea come whatsapp e la funzione videochiamata”.
Industria 4.0 e Covid: le tecnologie sperimentate nel lockdown che supporteranno la transizione al new normal e oltre
L’auditing virtuale sperimentato in fase di lockdown proseguirà anche in futuro. “Non solo continueremo a praticarlo, ma ci stiamo già muovendo per implementarlo al meglio, grazie un accordo con una società di software per un sistema di assistenza remota che sfrutta il principio degli smart glasses e consente controlli e ispezioni a distanza, con il consenso alla sperimentazione da parte degli enti di certificazione”, prevede Bottinelli. L’applicazione sarà estesa anche ad attività di ispezione su macchine strategiche di impianti all’interno del ciclo produttivo con benefici attesi sia in termini di costi e sia di efficacia manutentiva.
Anche la virtualizzazione e tematiche di digital twin, non solo si sono dimostrare utili per controllare da remoto i siti produttivi ma sempre più lo saranno in un’ottica di predictive maintenance per gestire il ciclo di vita e per stimare il deterioramento della macchina in specifiche condizioni, oltre che facilitare il lavoro in ambienti ostili e complicati, come sostiene Parabiaghi.
Tecnologie sperimentate in fase di lock-down saranno utilizzate anche in futuro per garantire ambienti di lavoro puliti e ordinati, a garanzia della salute, come spiega Dario Colozza , e-industries Global Advisory and Optimization Solutions Energy Efficiency di Enel: “Abbiamo impiegato il sistema di monitoraggio dei reattori energetici (elettricità e gas) e una soluzione per il controllo remoto dei sistemi di climatizzazione, cercando di ottimizzarlo”.
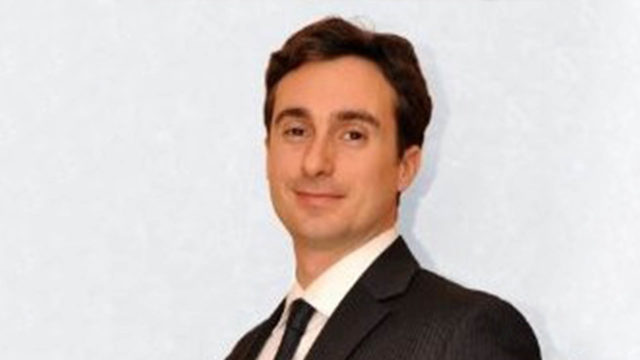
Adattando tecnologie pre-esistenti, Enel ha confezionato kit assemblati con sensori di campo (temperatura, umidità, CO2…) per indicare lo stato degli ambienti e fornire il monitoraggio in tempo reale dello stato dell’edificio. “Siamo inoltre in grado, tramite le nostre soluzioni di controllare da remoto la climatizzazione e, via ML, modulare in maniera preventiva le portate d’aria, per garantire il giusto livello qualità dell’aria.
Un ruolo importante durante la diffusione del Covid e non solo hanno svolto le tecnologie relative a Industria 4.0 che prese singolarmente sono però insufficienti per portare nel new normal un cambiamento esteso dei processi industriali. Lo sostiene Guido Porro, Euromed Managing Director e Amministratore Delegato di Dassault Systèmes.
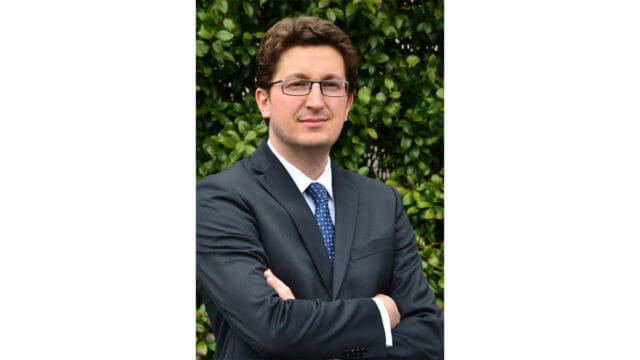
“Cosa contraddistingue questo Rinascimento industriale manifatturiero e tecnologico di cui tanto si parla?” – si chiede – Come Dassault Systèmes la risposta è la piattaforma tecnologica che riesce a far comunicare con lo stesso linguaggio non tanto le singole tecnologie quanto le persone, in azienda e fra aziende”. Le singole tecnologie esistono da anni e certo hanno visto una maturazione significativa ma da sole non giustificano il salto di produttività promesso da Industria 4.0. “Serve una piattaforma che faccia dialogare le persone (l’ingegnere, il designer, l’uomo di marketing), abilitando una nuova creatività che non solo aiuti a risolvere i se pur rilevanti problemi contingenti e verticali ma abiliti nuovi modelli di business anche per le PMI a cui possono accedere grazie alla logica di piattaforma e la disponibilità su cloud”.
Quali ricadute organizzative nel new normal?
“Vorrei mantenere tutto tranne i guanti e mascherine” – sostiene Salina – È ancora presto per tirare le conclusioni ma, grazie agli investimenti in tecnologia Castel ha potuto continuare a lavorare nel pieno della crisi, tenendo aperti gli uffici, e mantenere i contatti con i clienti”. Sono state eliminate tutte le riunioni in presenza e sostituite con meeting via web, con ricadute in termini di efficacia, eliminazione della reportistica, più puntualità e rapidità, minori tempi di trasferimento. “D’ora in poi si dovrà trovare il giusto equilibrio fra lavorare da casa e in azienda, continuando a operare in una nuova dimensione più vicina alle persone e alle loro esigenze”.
Uso intenso del lavoro da remoto anche per Enel con 37mila persone (su 80mila dipendenti) che da marzo stanno lavorando da casa; 30mila continueranno a farlo fino a fine anno, mentre alcune persone rientreranno con controllo accessi tramite telecamere termiche e sistemi di protezione. “La remotizzazione completa, mantenendo l’operatività nel day-by-day e il livello di servizio, è stata possibile grazie alle implementazioni digitali”, sottolinea Colozza.
Secondo Bottinelli il ricorso allo smart working in un’azienda tradizionale come Italcementi diventerà un caposaldo anche per le strutture di back office con benefici per i dipendenti, in termini di qualità della vita, per l’azienda, in termini di saving.
Per concludere con Dal Pozzo: “Tutte le aziende che applicano i paradigmi che si rifanno alla cultura giapponese (per semplificare sistema Toyota) hanno trovato un beneficio importante anche in un momento di cambiamento come questo. Le aziende sono fatte di persone e le persone vanno messe al centro anche in un momento in cui la sicurezza è al primo posto. Gli strumenti lean hanno favorito la riconfigurazione del processo per riportare a quegli standard di efficienza che inevitabilmente le aziende devono avere”.
Produrre in sicurezza, dunque, con standard efficienza e di qualità pre-covid, grazie alla messa al centro delle persone e a processi stabili e robusti.