Pirelli è una grande azienda italiana che non ha bisogno di presentazione. Ci limitiamo a ricordare il contesto produttivo di Pirelli Tyre: 19 stabilimenti in oltre 10 Paesi distribuiti in 4 continenti e circa 30mila addetti, due-terzi dei quali nella componente manifatturiera.
L’azienda ha avviato da due anni un percorso di trasformazione digitale delle attività manifatturiere che punta a interconnettere gli asset produttivi a monte con i fornitori e a valle con i clienti, entrambi già utenti dei sistemi Pirelli. Lo illustra Mario Apollonio, Head of Industrial Systems Pirelli Tyre, presentando l’esperienza della sua azienda in occasione del convegno Industria 4.0: la grande occasione per l’Italia, organizzato dall’Osservatorio Industria 4.0 del Politecnico di Milano.
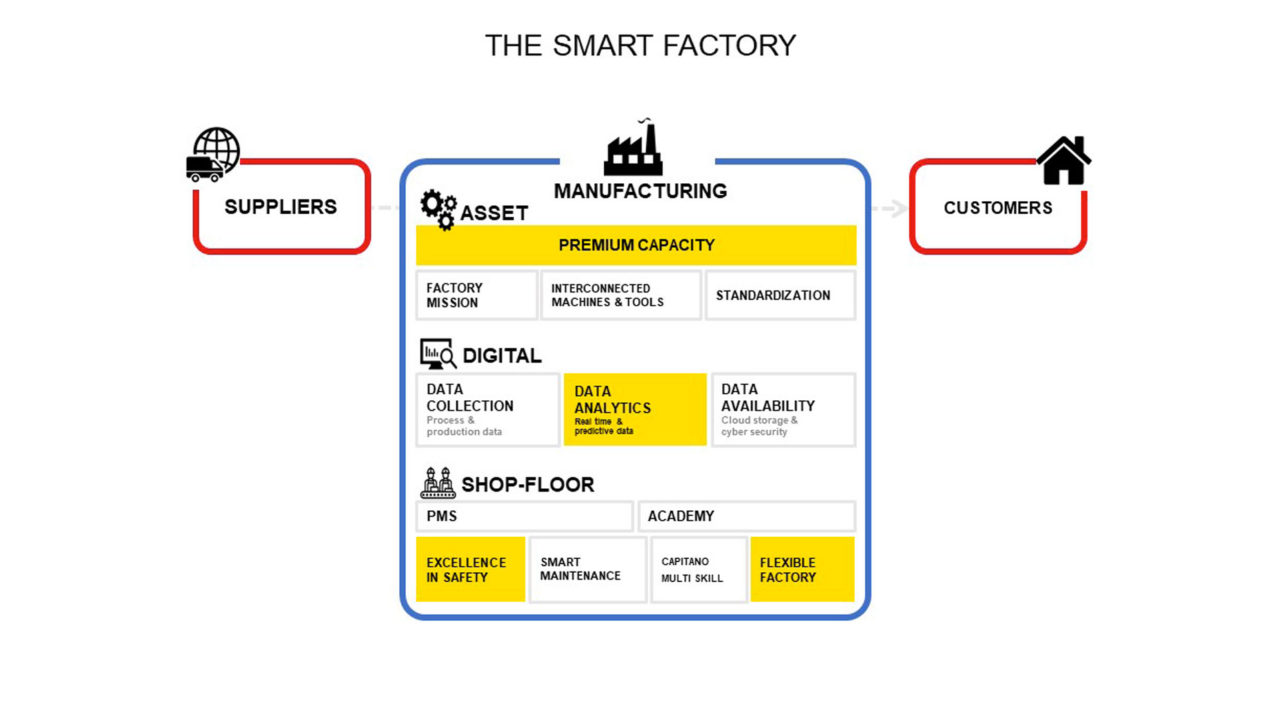
Per attuare il percorso di digitalizzazione, Pirelli sta operando su tre linee principali: il lavoro di interconnessione degli asset; le problematiche relative alla raccolta, la gestione e la distribuzione dei dati; gli aspetti connessi più strettamente alla fabbrica e, soprattutto, alle persone che vi operano.
Apollonio mette in evidenza l’importanza della standardizzazione che consente di garantire non solo la qualità dei dati e la loro comparabilità ma, al tempo stesso, tenere sotto controllo i costi. “Il cuore della digitalizzazione è la gestione del dato”, sottolinea. Il primo aspetto è garantire la corretta raccolta dei dati, gestendone il processo e la produzione. “Le macchine, data l’attuale capillarità della sensoristica, oggi possono raccogliere molti più dati che in passato – precisa Apolllonio – Questi devono essere memorizzati e analizzati sia dai sistemi automatici sia, soprattutto, dalle persone”. Ma anche grazie ai tool dedicati è sempre più facile interpretarli. “Ci siamo specializzati nell’utilizzo di Excel per poi renderci conto del suo limite dimensionale nella gestione dei dati – commenta – Oggi abbiamo bisogno di tempi rapidi per gestire grandi quantità di dati, trovarne le correlazioni, rendendo visibili sia quelle forti sia quelle deboli”. Qui entrano in gioco nuovi strumenti di analisi e i data scientist.
I dati devono essere resi disponibili a tutti, garantendo al contempo la sicurezza: “Servono dunque, a supporto, sia politiche aziendali adeguate, sia infrastrutture per memorizzare i dati in cloud e renderli accessibili, sia strumenti e politiche di cyber security”, precisa il manager.
Il successo del processo di digitalizzazione “viaggia sulle gambe delle persone”, soprattutto quelle 20mila circa che, in Pirelli, operano nell’ambito della manifattura. Da loro soprattutto può derivare l’eccellenza nel campo della sicurezza e della manutenzione intelligente che caratterizza una fabbrica flessibile.
Indice degli argomenti
La digitalizzazione in tre passi
Una volta che si dispone dei dati non basta renderli visibili e disponibili a tutti. Affinché vengano utilizzati in modo efficace sono indispensabili, secondo Apollonio: un training generalizzato per ottenere un’adeguata comprensione, la fruizione e il loro utilizzo ottimale; la disponibilità di tool di analisi dati on-line; la virtualizzazione e il machine learning.
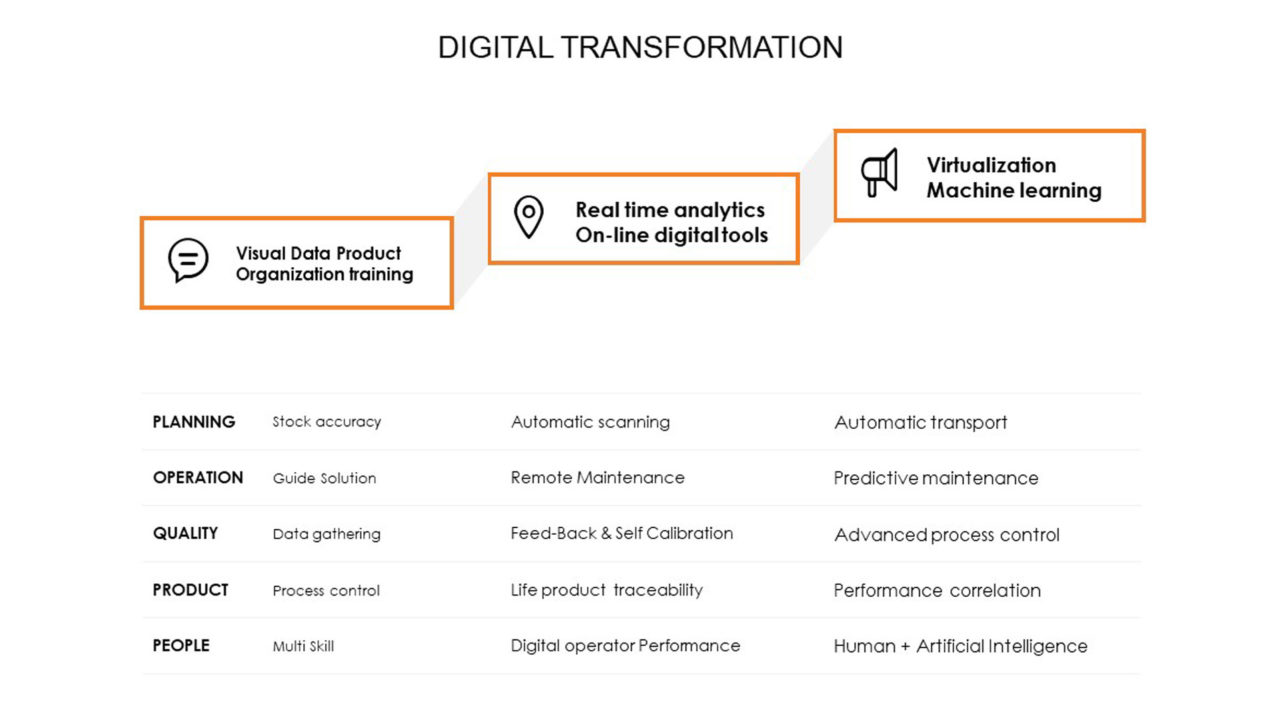
- È indispensabile organizzare innanzi tutto un training multilivello. “Non si può pensare di formare solo la parte “bassa”, dove ci sono persone più giovani e predisposte al cambiamento, se non si è prima stati capaci di convincere il management, in tutte le fabbriche e nelle diverse aree culturali, della necessità di portare avanti il cambiamento – sostiene Apollonio – Questo sforzo ci ha impegnato negli ultimi due anni nei diversi Paesi”.
- Servono strumenti e metodologie che aiutino a essere più vicini al dato e avere la capacità di reagire rapidamente. “Vogliamo evitare le analisi ex-post che segnalino i problemi dopo che sono avvenuti e che dovrebbero servire, nella migliore delle ipotesi, a evitarli in futuro – spiega Apollonio – Tutto questo ci obbliga ad avere infrastrutture migliori, tool online, persone pronte a leggere le informazioni”. L’idea alla base del percorso di Pirelli è che le persone debbano conoscere la provenienza dei dati e dunque non essere solo utenti dei sistemi. “L’operatore va formato non solo sulla mera funzionalità della macchina, ma anche sulla modalità di generazione del dato, sulle sue caratteristiche, sulla sua pulizia…”, sottolinea.
- Il terzo punto che si vuole raggiungere nel medio periodo è la virtualizzazione, sia per quanto riguarda la gestione della singola macchina sia per la fabbrica, per realizzare processi produttivi capaci di “predire” se stessi. L’obiettivo è realizzare una fabbrica che sappia modificare i propri schemi di produzione in funzione delle diverse performance delle macchine, che non sempre sono allineate allo schema teorico.
In questo campo, Pirelli ha già avviato alcune sperimentazioni di virtualizzazione, limitate, per ora, alle attività di training, considerate particolarmente significative visto che “la formazione garantisce efficienza, motivazione delle persone e sicurezza”, come evidenzia Apollonio. La macchina su cui le persone devono essere addestrate viene virtualizzata e portata in un simulatore, mentre le persone vengono dotate di strumenti di interazione con il sistema. Gli addetti da formare possono così prendere confidenza con la macchina, capirne i movimenti e le regole di sicurezza. Lo stesso metodo viene utilizzato anche per affrontare alcuni temi relativi alla qualità.
Gli interlocutori del percorso di digitalizzazione
Quanto fin qui detto viene declinato in relazione a cinque attori principali della fabbrica, che rappresentano i clienti interni: Planning, Operation, Quality, Product e People.
Apollonio ricorda che in ambito pianificazione si può ancora migliorare “l’accuratezza maniacale” fin qui raggiunta per arrivare all’Automatic transport, ossia la capacità dei trasporti dei prodotti di adattarsi alla produzione e di anticiparne le necessità.
In ambito qualità, se fino a cinque anni fa si operava con un controllo statistico, ora ci si focalizza sulla raccolta dei dati di processo, sulla capacità di dare dei feedback il più possibile automatizzati (partendo da feedback manuali per capire quali possano essere automatizzati e portarli dentro il processo) fino alla calibrazione automatica, per consentire alla macchina di correggersi, all’inizio su aspetti facili come velocità, pressione… e poi, quando le correlazioni vengono trovate, eventualmente fermarsi e segnalare il possibile insorgere di problemi.
Verso le persone viene infine adottata una strategia multiskill per mettere gli operatori in grado di reagire velocemente, anche grazie a competenze su più livelli. “La fabbrica del futuro non vedrà più persone fisse a una postazione, ma persone che si muovono nell’impianto, avendo a disposizione i dati per vedere e intervenire sui problemi”, prevede Apollonio.
Le persone sono i protagonisti principali del percorso di digitalizzazione: “Dobbiamo riuscire a trasferire, soprattutto alle persone operative, il senso della trasformazione digitale in termini di continuità di cambiamento e non in una logica disruptive – sottolinea Apolllonio, che precisa – Concordo con la necessità di dare segnali di cambiamento forte [ndr: il riferimento è ad alcuni interventi in occasione del convegno sopra citato], ma quando si va verso una fabbrica con persone abituate a lavorare in continuità con i sistemi, bisogna spiegare bene la prospettiva e abituarle gradualmente al cambiamento”. Il percorso di Pirelli prevede l’adozione di sistemi digitali di cambiamento lean (continous improvement e people engagement), per garantire la motivazione, e l’Academy interna, che sarà sviluppata su temi specifici come l’utilizzo del software e dell’analitica. “È utile soprattutto far capire come l’interpretazione dei dati possa essere utile nel lavoro di tutti i giorni”, conclude Apollonio.