Tecnoacciai è una tipica azienda manifatturiera italiana da 8 milioni di fatturato e meno di 20 dipendenti che lavora su commessa: taglia acciaio (4700 tonnellate l’anno) per aziende clienti che producono stampi a freddo e a caldo. Fa parte del gruppo internazionale Euromeccanica (da 100 milioni di fatturato) che ha svolto un ruolo importante nel progetto di trasformazione a smart factory, fornendo alcune competenze fondamentali come quelle dell’IT manager di gruppo, mentre non è prevista una funzione IT interna; la componente tecnologica e le soluzioni sono state sviluppate in collaborazione con partner esterni all’interno di un percorso condiviso.
“L’azienda, da quando ha iniziato il processo di trasformazione tre anni fa, ha completamente cambiato pelle – ricorda l’amministratore delegato Enzo Bonato di Tecnoacciai – Il cambiamento si è visto soprattutto sulle persone, coinvolte fin dall’inizio nel percorso: i ragazzi non sono più quelli di prima ed è molto cambiata la qualità del loro lavoro in azienda”.
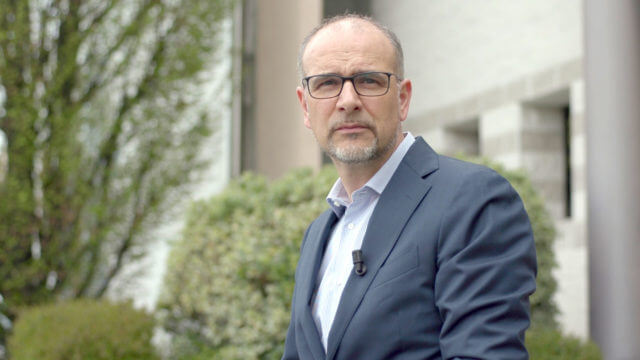
Per portare l’azienda a diventare una smart factory, sono stati messi in campo solo quattro dei nove step previsti all’interno del programma Industria 4.0, ossia quelli più adatti all’attività dell’azienda e ai suoi obiettivi: focalizzare e monitorare, normalizzare, dematerializzare, intercettare e ‘triggerare’.
“La dematerializzazione è stata fondamentale non solo per eliminare la carta, con importanti ricadute ecologiche, ma soprattutto per i vantaggi offerti dalla digitalizzazione del dato che può essere utilizzato da più persone (a differenza del foglio di carta) ed è più facilmente gestibile”, sottolinea Bonato. I 20mila fogli che circolavano in fabbrica sono stati eliminati, sostituiti dalle informazioni su tablet in dotazione a ciascuna macchina. L’ambiente di lavoro è completamente allineato al paradigma Industria 4.0: sia le macchine già presenti, sia quelle nuove, acquistate per la messa a punto del progetto, sono allineate in termini di sensori e tablet al paradigma Industria 4.0.
Indice degli argomenti
Integrazione e monitoraggio in Tecnoacciai
Il sistema MES (Manufacturing Execution System), sviluppato ad hoc e integrato con il gestionale, offre visibilità in tempo reale dello stato della produzione e controllo delle operazioni di fabbrica.
Gli operatori di reparto vedono in tempo reale, sui grandi monitor presenti in fabbrica, lo stato delle macchine, che viene replicato negli uffici: il verde evidenzia la macchina che sta lavorando (con l’indicazione dell’ordine in esecuzione), il rosso indica la macchina ferma (e le eventuali cause), mentre il celeste indica la macchina in approntamento per la successiva lavorazione programmata: “Anch’io ho la stessa visione sullo smartphone e posso avere dunque sotto controllo la situazione della fabbrica da qualunque luogo”, precisa il CEO.
I dati raccolti si integrano con il gestionale rendendo possibile verificare le ore in cui ciascuna macchina e l’operatore hanno lavorato, cosa è stato tagliato, quali ordini sono stati portati a termine. È anche possibile valutare il livello di utilizzo di una macchina per decidere, ad esempio, se si deve acquisire una macchina nuova e prevedere le necessità di manutenzione.
Il sistema di KPI messo a OEE (Overall Equipment Effectiveness), legato a parametri come qualità, disponibilità e performance, aiuta a valutare il raggiungimento degli obiettivi nel percorso di trasformazione a partire dalla situazione di partenza.
Un magazzino intelligente per una smart factory
Un significativo aumento di efficienza è derivato anche dallo step previsto da Industria 4.0, intercettare e triggerare, che in Tecnoacciai si è tradotto in una elevata efficienza nella gestione del magazzino derivante da una stretta interazione uomo-macchina.
“Un lavoro relativamente semplice che prevede solo tagli di acciaio”, come lo descrive Bonato, è stato ottimizzato soprattutto in termini di logistica, semplificando la ricerca del materiale. Tutti i pezzi nel magazzino sono infatti classificati e monitorati.
I pezzi più piccoli disponibili vengono misurati nel cassetto in cui sono riposti nelle loro tre dimensioni da uno scanner e classificati di conseguenza. Il sistema, sulla base dei requisiti dell’ordine in lavorazione, propone all’operatore i pezzi adatti per le esigenze del cliente andando a ottimizzare il taglio; fra i pezzi proposti dalla macchina l’operatore sceglie. “È un esempio di interazione collaborativa fra uomo e macchina”, sottolinea Bonato.
Uno dei grandi monitor presenti nel magazzino, illuminandosi segnala la presenza del pezzo scelto; nel caso sia contenuto in un cassetto, questo si apre e un raggio laser indica il pezzo scelto, semplificando le operazioni e i tempi di ricerca.
Un investimento con elevati margini di ritorno
Il progetto in Tecnoacciai è costato 2 milioni di euro in 2 anni, corrispondente a circa il 13% del fatturato, il 47% dei quali recuperabili con vantaggi fiscali, come l’iper-ammortamento previsto dal piano Industria 4.0, finanziamenti per ricerca e sviluppo e la cosiddetta legge Sabatini.
“La maggiore efficienza ha certo riflessi sul conto economico, ma ciò che più conta è la trasformazione che ha prodotto un aumento del valore dell’azienda grazie al miglioramento dei sistemi di controllo e a un personale più motivato”, afferma Bonato, che sottolinea l’importanza di rendere le persone protagoniste del cambiamento. “I nostri ragazzi hanno conseguito sul campo i gradi di Industry 4.0 e sono passati da svolgere semplice ‘manodopera’ a ‘mentidopera’”. La scelta è stata infatti da un lato di affidarsi a partner esterni, come già detto, per lo sviluppo del progetto, ma dall’altro di coinvolgere i responsabili di produzione e i lavoratori in unpercorso di crescita condiviso fin dalle prime fasi, verificandone la disponibilità al cambiamento.
I partner con cui è stato condiviso il percorso sono stati Phase del gruppo Infoteam per la componente Mes e integrazione con il gestionale e Considi per la Manutenzione programmata e l’implementazione dei principi della lean production.