Il progetto dal titolo Schneider Electric per azienda produttrice contenitori in vetro (risultato finalista ai Digital360 Awards 2021 per la categoria Soluzioni Infrastrutturali) è stato realizzato da Schneider Electric per garantire la continuità operativa in un contesto produttivo particolarmente delicato (forni ad alta temperatura, mantenuti a circa 1600°C per 365 giorni all’anno). Esso ha visto l’implementazione di una soluzione “micro data center”, costituita da un armadio blindato e diversi accorgimenti per riportare in piccolo tutte le best practice che normalmente vengono impiegate nei grandi datacenter.
Indice degli argomenti
Perché la soluzione di Schneider Electric
L’intero processo del produttore di vetro è controllato da un sistema di supervisione che monitora le condizioni di funzionamento e garantisce la sicurezza. Il materiale in fusione arriva a temperature che sono prossime alle temperature massime sostenibili dai forni. Non è perciò ammesso perderne il controllo, si metterebbe a rischio un investimento aziendale del valore di diverse decine di milioni di euro.
L’infrastruttura IT sostiene il processo produttivo e abilita il sistema di controllo. Rappresenta quindi un servizio essenziale. La sua costante disponibilità è necessaria sia per la continuità operativa, sia per evitare ingenti danni.
La strategicità dell’infrastruttura IT negli ultimi anni è anche accresciuta. Sempre più dati vengono raccolti da tutta la linea produttiva per alimentare analytics e intelligenza artificiale.
Il processo del vetro è molto complesso. L’efficienza produttiva dipende da numerosi parametri di temperatura, pressioni e portate lungo la linea. Imparare da questi dati è fondamentale per implementare azioni di miglioramento del prodotto e l’abbattimento degli scarti produttivi.
Infine, l’infrastruttura IT assicura anche la conservazione delle preziose ricette produttive, la tracciabilità del prodotto e i dati storici di produzione e di performance. Indubbiamente rappresenta un’infrastruttura critica per l’azienda, non solo da proteggere in termini di cyber-security, ma a cui dare massima resilienza in senso ampio.
L’architettura IT normalmente utilizzata in ogni stabilimento è realizzata con due server rack, installati in un locale tecnico dedicato alle apparecchiature IT e configurati in ridondanza. La valutazione fatta dal direttore IT e dal direttore di produzione, è che detta soluzione necessitava di essere ulteriormente migliorata, evitando di avere i due server installati nel medesimo locale, poiché un evento critico in questo ambiente può compromettere l’intero sito. L’orientamento iniziale era di realizzare un secondo locale tecnico, per installare il secondo server in una posizione lontana dal primo. Soluzione che però si scontrava con la difficoltà di ricavare questo spazio in ambito produttivo. Essendo funzionale al processo produttivo, non sono invece accettabili data center remoti o servizi cloud.
Il progetto è stato realizzato perché capace di rispondere alle seguenti esigenze dell’utente finale: risolvere il problema della mancanza di spazio per un nuovo locale tecnico; evitare importanti costi di realizzazione, con un risparmio complessivo valutato circa -30%; tempi rapidi per l’implementazione e flessibilità di posizionamento nel sito industriale; affidabilità, grazie alla raccolta di dati dall’infrastruttura e al monitoraggio predittivo; possibilità di attivare a un servizio di assistenza 24/365 da parte di Schneider Electric abilitato dai dati disponibili anche in remoto.
La tecnologia implementata
Dopo una fase di valutazione delle esigenze e di verifica dello stato dell’infrastruttura in campo, la proposta è stata quella di implementare una soluzione “micro data center”, costituita da un armadio blindato e diversi accorgimenti per riportare in piccolo tutte le best-practice che normalmente sono impiegati nei grandi datacenter.
Il micro datacenter configurato si presenta come un armadio delle dimensioni di circa 80 cm di larghezza, 120 di profondità e 200 di altezza, di elevata resistenza meccanica, che è possibile posizionare in un ambiente già disponibile per altri usi. Oltre ad ospitare gli apparati IT su rack 19”, è stato integrato con:
- sensori di temperatura e umidità per il monitoraggio continuo delle condizioni ambientali e di funzionamento delle apparecchiature;
- apertura di sicurezza da utente autorizzato tramite badge;
- registrazione accessi con telecamera ad alta risoluzione;
- UPS ad alta efficienza, per garantire continuità e protezione da problematiche di qualità dell’alimentazione elettrica;
- distribuzione dell’energia con monitoraggio assorbimenti elettrici e comando da remoto del singolo dispositivo alimentato.
Tutti i dati prelevati dal micro datacenter e dalle apparecchiature contenute vengono portati a una piattaforma di monitoraggio con analytics. Qui i dati vengono continuamente analizzati per ottenere predittività, in modo da riconoscere potenziali anomalie di funzionamento e poterle risolvere prima che queste diventino guasti.
L’implementazione, partita da un primo sito produttivo di test, è stata poi adottata in altri 5 in Italia.
L’esperienza italiana è stata anche considerata come pilota dal dipartimento IT corporate del cliente, quale soluzione standardizzata per portare massima resilienza anche agli altri siti produttivi nel mondo.
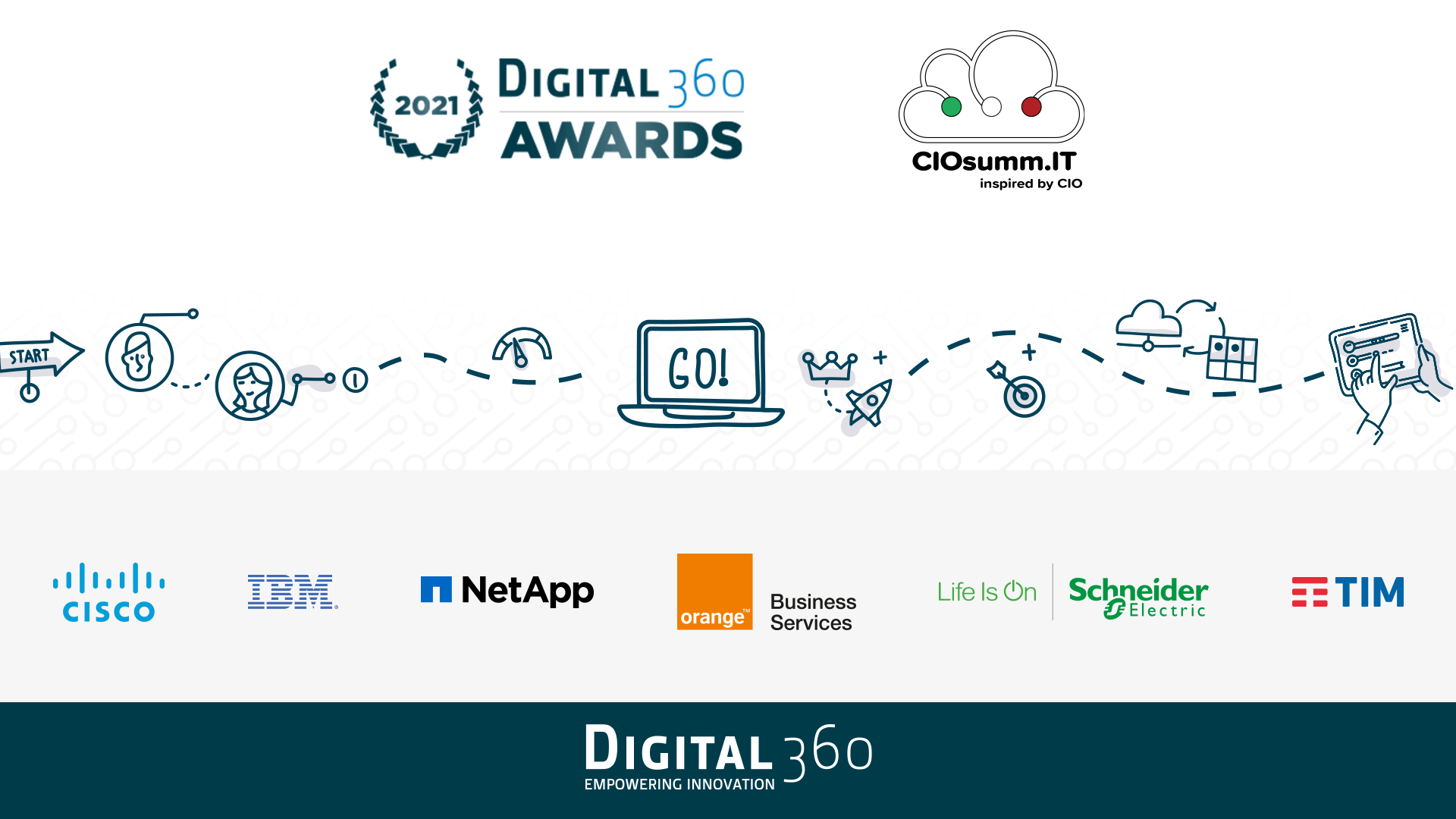