I vantaggi della stampa 3D sono stati al centro dell’attenzione durante la pandemia: la capacità di passare direttamente dalla progettazione alla produzione ha consentito risposte rapide alle esigenze mediche, mentre le stampanti geograficamente distribuite possono consentire la produzione ovunque si verifichi un’esigenza. Questa aumentata consapevolezza sulla stampa 3D potrebbe accelerare l’espansione del settore: già alcuni anni fa c’è stato un hype circa la stampa 3D, che avrebbe dovuto essere presente in ogni casa e consentire alle industrie di produrre ogni cosa; nella realtà questa tecnologia si affianca e integra quelle tradizionali, offrendo un modo più agile di definire una catena di approvvigionamento.
L’impellente necessità, insieme alle limitazioni agli spostamenti, ha messo in evidenza l’incredibile velocità con cui chi era dotato di una stampante 3D, fosse un maker a casa, un’impresa in officina o in laboratorio, si è attivato ed è stato in grado di prendere un’idea e trasformarla in un prodotto finito nel giro di ore. Mentre uno stampo a iniezione può consentire la rapida produzione di milioni di parti, ma la produzione dello stampo iniziale richiede molto tempo, con la stampa 3D invece la produzione può iniziare immediatamente, seppur in quantità più ridotte.
Indice degli argomenti
Valvole per respiratori ospedalieri a tempo record: Isinnova
Una delle notizie che maggiormente hanno colpito l’opinione pubblica durante l’apice della pandemia di Covid-19 in Italia a metà marzo è stata sicuramente quella delle valvole per respiratori ospedalieri realizzate in tempo record da un’azienda bresciana, Isinnova. L’Ospedale di Chiari si è trovato nell’impossibilità, data dall’urgenza di estrema necessità, letteralmente questione di vita o di morte, di approvvigionarsi di un pezzo di ricambio necessario ai respiratori, del valore di pochi euro in sé, ma facente parte di un meccanismo complesso, molto costoso e, soprattutto, correttamente certificato e omologato per uso medico ospedaliero.
[A questo link l’intervista a Massimo Temporelli, che ha collaborato con Cristian Fracassi di Isinnova allo sviluppo del progetto]
In sole ventiquattr’ore Isinnova è riuscita a fornire oltre 100 particolari: certo, le norme ospedaliere sono state scavalcate, insieme a quelle brevettuali, in nome di un interesse superiore, la salute dei pazienti in condizioni critiche. A onor del vero, i responsabili di Isinnova hanno tentato immediatamente di contattare il fornitore ma, non ricevendo risposta, hanno deciso comunque di procedere.
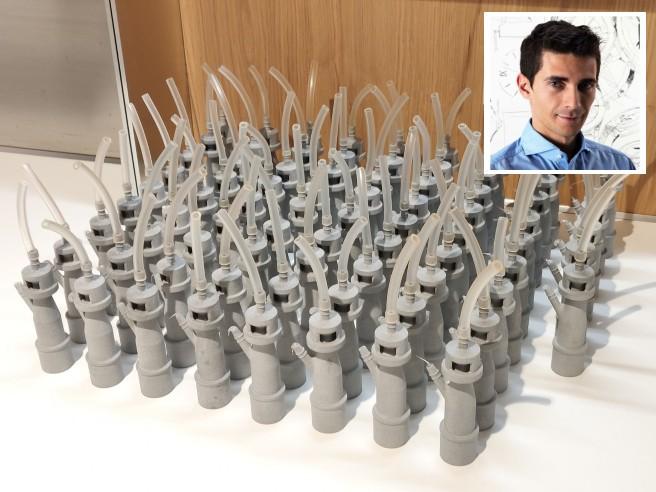
Foto 1 – Alcuni dei connettori per respiratore polmonare realizzati da Isinnova tramite stampa 3D
La notizia di questa esperienza è passata poco dopo dall’Ospedale di Chiari al dottor Renato Favero, ex primario dell’Ospedale di Gardone Valtrompia, che ha contattato Isinnova per riadattare una maschera da snorkeling, ideata e commercializzata da Decathlon, come maschera respiratoria ospedaliera d’emergenza C-PAP (Continuous Positive Airway Pressure) per terapia sub-intensiva. In questo caso, Decathlon ha collaborato fornendo immediatamente i modelli CAD della maschera Easybreath, accelerando il lavoro di prototipazione del nuovo componente per il raccordo al respiratore, chiamato valvola Charlotte, e che, stampato rapidamente in 3D, è stato positivamente testato ancora all’Ospedale di Chiari.
Questa esperienza, in contemporanea con la copertura mediatica internazionale di cui godeva sfortunatamente il nostro Paese in quei giorni, ha scatenato letteralmente una valanga globale di iniziative analoghe che, prima partite dal mondo dei maker, ha poi finito per coinvolgere aziende tradizionali, anche molto note, pur se in tutt’altro ambito.
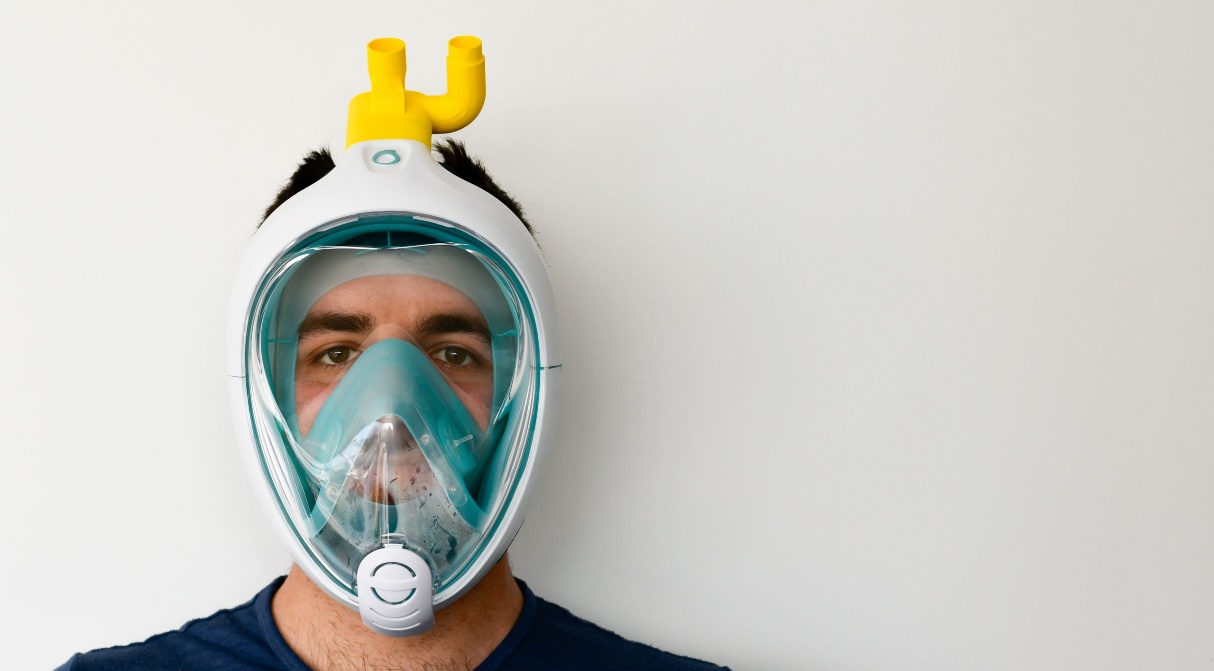
Foto 2 – La valvola Charlotte di Isinnova (in giallo) sulla maschera EasyBreath di Decathlon
Dopo la notizia delle maschere Decathlon, anche l’italianissima MARES, azienda ligure produttrice di attrezzatura subacquea, ha attivamente contribuito alla creazione di adattatori per una maschera da snorkeling analoga. All’azienda Mira Meccanica, che si era resa disponibile a realizzare i primi prototipi funzionali (con tecnologia HP Multi Jet Fusion, utilizzando il materiale PA12), nel giro di pochi giorni si sono aggiunte: Protoflash, Pariani, FPZ, PIUSI, Campetella Robotics Center, Ferrari, Everex, Juno Design, SB3 e Innovamec. Più di 1.200 collettori e quasi 1.000 maschere assemblate sono state consegnate a tantissimi ospedali in tutta Italia (tra cui Parma, Bologna, Imola, La Spezia, Genova, Rapallo, Brescia, Pinerolo).
Vale in ogni caso la pena riportare quanto presente sul sito che descrive questa iniziativa: “Ribadiamo che l’idea si rivolge a strutture sanitarie e vuole aiutare a realizzare una maschera d’emergenza nel caso di una conclamata situazione di difficoltà nel reperimento di fornitura sanitaria ufficiale, solitamente impiegata. Né la maschera né il raccordo valvolare sono certificati e il loro impiego è subordinato a una situazione di cogente necessità. L’uso da parte del paziente è subordinato all’accettazione dell’utilizzo di un dispositivo biomedicale non certificato, tramite dichiarazione firmata”.
Analoga comunicazione è giunta nei giorni successivi dalla stessa Decathlon.
Le valvole tipo Charlotte sono valvole mono-paziente, che trasformano una maschera da snorkeling in maschere d’emergenza non certificate utili in mancanza delle maschere C-PAP utilizzate in terapia sub-intensiva. La produzione di questi pezzi deve comunque essere effettuata da personale competente, sia dal punto di vista medico che ingegneristico (Quali sono i protocolli di emergenza da seguire? Che materiali utilizzare? Che tolleranze occorre rispettare? Si è provata la resistenza del pezzo?).
Se, da un lato, lo sforzo era mosso da una vitale necessità (nei reparti non c’era una maschera C-PAP per letto), dall’altro, la buona volontà non doveva comunque intralciare il personale medico: maschere e valvole devono essere abbastanza resistenti perché lo stesso paziente, o il personale sanitario, possano metterle e toglierle più volte; la pressione all’interno della maschera deve rimanere positiva e quanto più costante, per essere utile a quel paziente secondo le indicazioni prescritte. Per questi motivi, ad un certo punto, si è creato addirittura un eccesso di offerta: centinaia di makers hanno iniziato a produrre valvole, ovviamente di qualità molto variabile, per donarle, anche quando gli ospedali ne avevano già in quantità sufficiente oppure mancavano le maschere con cui poterle utilizzare. Pertanto le AUSL hanno chiesto il blocco degli invii anche per non aggravare la logistica, già ampiamente sotto stress.
Un esempio: la maggior parte dei maker utilizza stampanti a tecnologia FDM (Fused Deposition Modeling; oggettivamente la tecnologia più semplice ed economica tra quelle di fabbricazione additiva) e il materiale utilizzato più di frequente è il PLA (acido polilattico, un polimero di derivazione vegetale e biodegradabile a lungo termine). Un oggetto in PLA dovrà essere gettato dopo il primo utilizzo in quanto non è sterilizzabile (come il PET) e poco resistente alle soluzione alcoliche. Poiché tutti i dispositivi debbono essere disinfettati dopo ogni interazione con i pazienti, è fondamentale fornire dispositivi riutilizzabili.
Valvole per respiratori dalla IVAR
Una delle prime aziende a muoversi con estrema velocità e altrettanta competenza è stata la bresciana Ivar, che di valvole se ne intende, dal momento che progetta, sviluppa e realizza sistemi per il riscaldamento e impianti sanitari. Appresa la notizia dell’idea di Isinnova la sera di sabato 21 marzo, i responsabili di Ivar hanno immediatamente attivato i loro tecnici, già operativi domenica pomeriggio, riuscendo a stampare 21 coppie (Charlotte + Dave) che dopo sole 13 ore sono state consegnate a Isinnova. Ottimizzando successivamente il volume di stampa, Ivar è riuscita a creare lotti di stampa di 30 coppie in contemporanea, fornendo nei giorni successivi 500 kit.
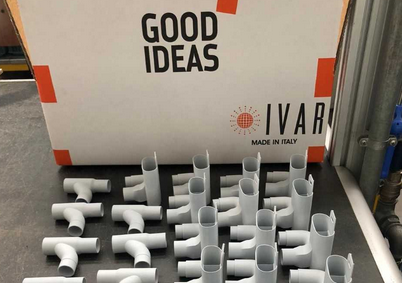
Foto 3 – I kit Charlotte + Dave realizzati da IVAR (tecnologia stampa 3D by HP Jet Fusion)
Valvole per respiratori: Lamborghini
Nella Motor Valley, Lamborghini ha collaborato con Siare Engineering International Group, unico costruttore nazionale di respiratori polmonari, per la realizzazione di simulatori polmonari, per stimare il corretto funzionamento del ventilatore polmonare prima dei test finali con apparecchi certificati. Il laboratorio 3D printing della casa di Sant’Agata Bolognese, lo stabilimento di produzione compositi e il reparto di ricerca e sviluppo hanno anche collaborato alla fabbricazione di visiere protettive mediche in policarbonato (realizzate tramite stampanti Carbon 3D e HP), arrivando a produrne fino a 200 al giorno.
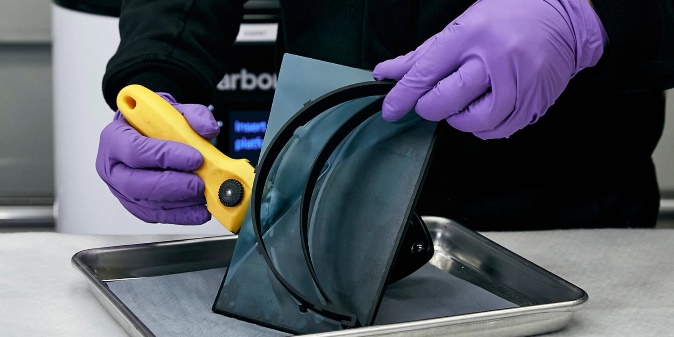
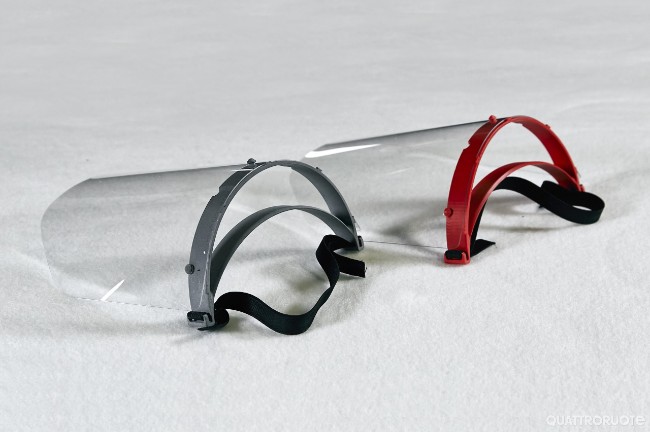
Foto — Le protezioni facciali realizzate da Lamborghini (tecnologia stampa 3D by Carbon 3D)
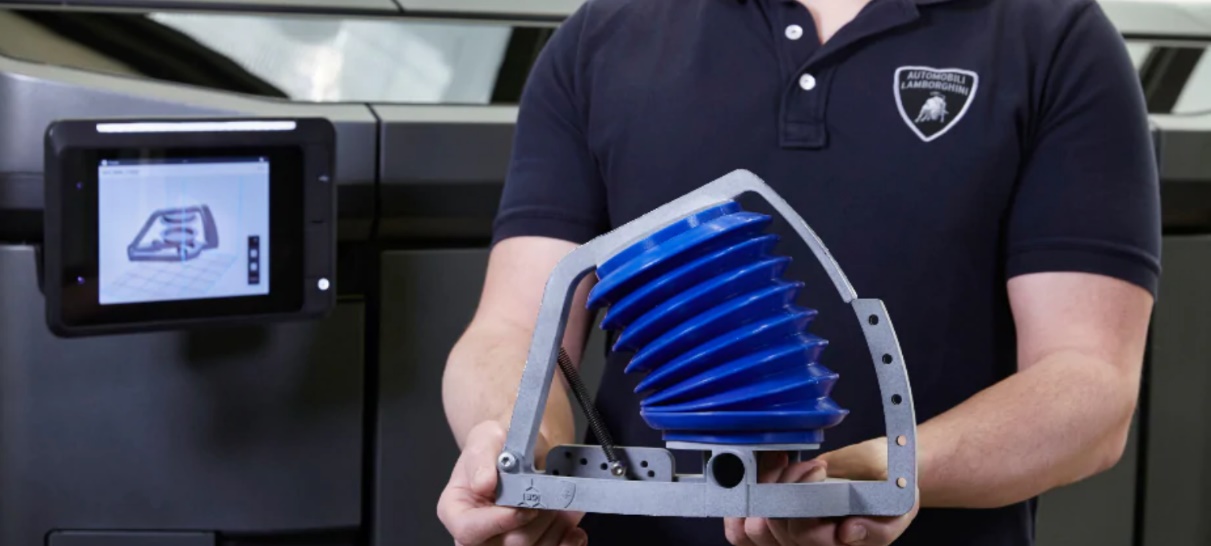
Foto – Il simulatore polmonare per ventilatore meccanico prodotto da Lamborghini (tecnologia stampa 3D by HP Jet Fusion)
Valvole per respiratori polmonari: Ferrari
Anche Ferrari non è stata da meno ed ha prodotto a Maranello valvole per respiratori polmonari e raccordi per maschere di protezione. Le avanzate stampanti 3D (Stratasys serie Fortus) del reparto “Costruzioni Sperimentali” hanno prodotto sia le valvole sviluppate dalla Mares, per creare dispositivi d’emergenza per i pazienti con crisi respiratorie, sia quelle per trasformare le maschere da snorkeling Decathlon in ausili a protezione del personale sanitario.
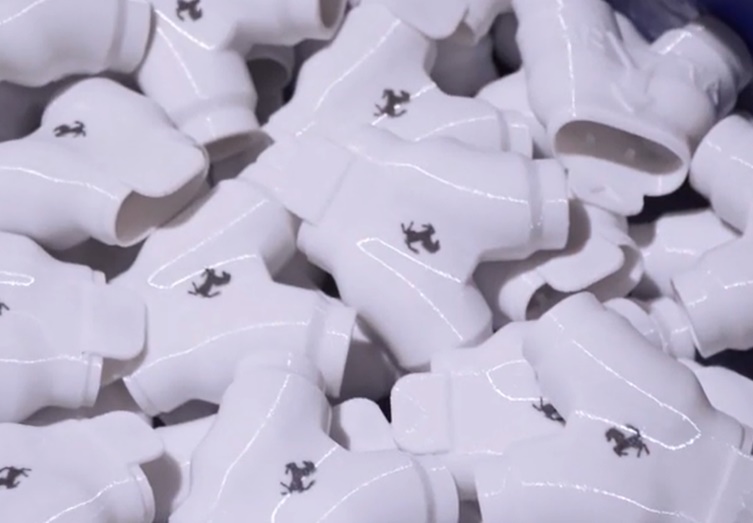
Foto 6 – Le valvole Ferrari per la maschera snorkeling di MARES (tecnologia stampa 3D by Stratasys Fortus)
Altri esempi di utilizzo di stampanti 3D a contrasto della pandemia
In tutto il mondo abbiamo visto, nel giro di qualche giorno, aziende manifatturiere e appassionati maker dedicarsi alla progettazione e realizzazione di strumenti in qualche modo utili nella battaglia contro Covid-19:
- apriporta;
- valvole per CPAP;
- visiere;
- accessori personali;
- componenti di ventilatori;
- mascherine.
Tra gli accessori personali, per esempio, le bande per scaricare la tensione degli elastici quando si indossa una mascherina: normalmente questi scaricano sulle orecchie, creando fastidio, se non addirittura lesioni, a chi le indossa per giornate intere, come medici, infermieri, personale del 118.
Un maker ha ripreso un progetto pubblicato da altri, apportando delle migliorie prima di ricondividerlo:
- ha rimosso il logo “perché è solo un altra superficie irregolare da stampare e covo di batteri e virus”;
- ha predisposto uno spazio vuoto per poter scrivervi il nome della persona;
- ha creato una seconda versione, incurvata per meglio adattarsi eventualmente alla base del collo.
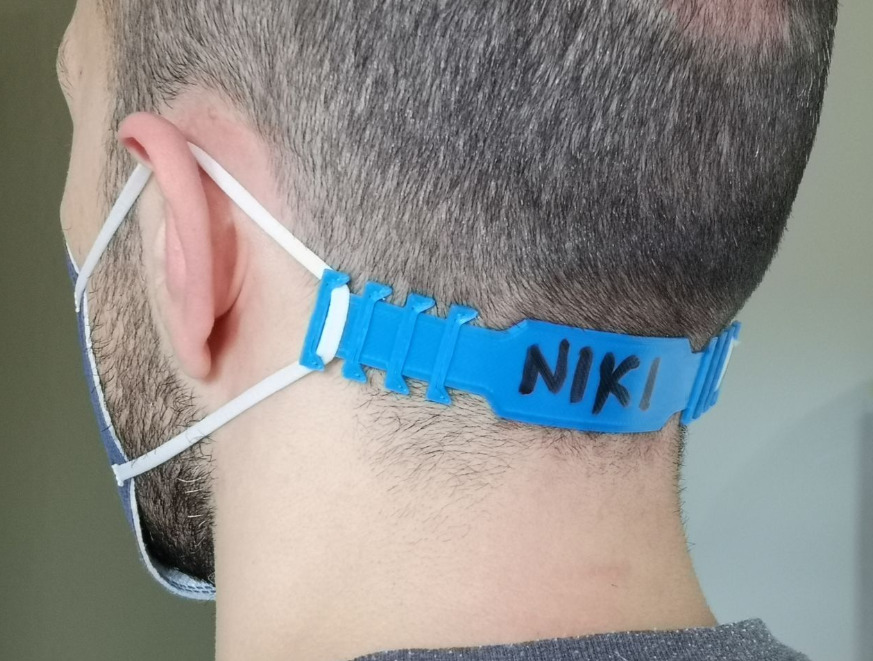
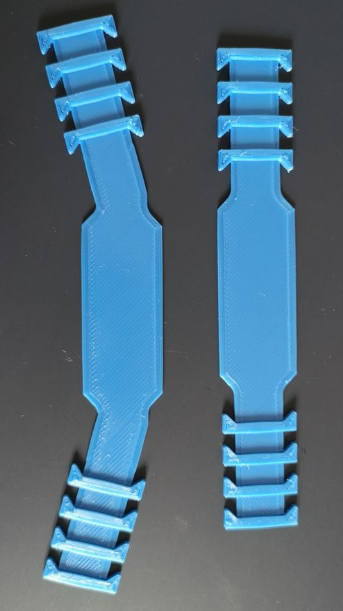
Foto – Banda per mascherina migliorata e resa disponibile gratuitamente (tecnologia stampa 3D: FDM)
La diffusione di queste iniziative è stata così massiccia e rapida che, a un certo punto, è diventato necessario riassumere chi stava facendo cosa, dove, come e per chi.
Un gruppo di appassionati americani ha creato un sito per “Evaluation of Open Source Ventilators” ove è stato raccolto ed analizzato un elenco di progetti per la realizzazione di ventilatori di emergenza in risposta a COVID-19, incentrato sull’open source gratuito. I progetti raccolti sono stati analizzati in termini di sette criteri che si sono ritenuti essenziali per distribuire con successo un ventilatore open source durante la pandemia di COVID-19:
- libera disponibilità;
- supporto delle community;
- producibilità;
- superamento di test di funzionalità;
- superamento di test di affidabilità;
- idoneità per COVID-19;
- facile applicazione in ambiente clinico.
L’obiettivo non è stato quello di classificare i progetti in sé, ma di far luce sullo stato di prontezza di questi progetti e forse identificare le criticità che devono essere affrontate prima che possano essere implementabili.
In Italia, per esempio, troviamo (da cui si può accedere anche all’iniziativa di cui sopra): “Makers for COVID-19 emergency” è un’iniziativa su base volontaria che mira a facilitare la collaborazione tra diverse community makers e a diffondere le potenzialità di una fabbricazione digitale, on-demand e distribuita in questa situazione d’emergenza. L’obiettivo è mettere in contatto esigenze del personale sanitario e volontario impegnato a fronteggiare l’emergenza con la capacità di risposta di fablab, makers e aziende desiderose di dare un contributo volontario alla lotta al coronavirus”.
Le possibilità della manifattura additiva
Della flessibilità in termini di reattività dal progetto all’oggetto si è già visto, ma la stampa 3D, o meglio, la manifattura additiva (AM, Additive Manufacturing), offre anche la possibilità di realizzare componenti con svariati materiali, il cui numero e varietà aumenta di anno in anno. Ci sono innanzitutto i materiali plastici, quelli visti fin qui, ma solo perché questi erano e sono i materiali degli oggetti prodotti nella battaglia contro il Covid-19 (oltre a essere anche i primi a essere stati storicamente utilizzati con queste tecnologie), ma già da diverso tempo è possibile realizzare in AM oggetti in metallo (acciaio, alluminio, titanio e leghe varie). I macchinari AM che realizzano oggetti in metallo non sono (ancora) alla portata di tutti, per competenze ed investimenti necessari, ed hanno, come limite attuale, la dimensione massima dei particolari producibili (ma già si stanno testando componenti per aerei, come parti di motori a jet, telai di sedili e tanto altro) ed il costo unitario dei particolari prodotti, se comparati con le tradizionali tecnologie di asportazione di truciolo, formatura, fusione ecc.
Per quanto non sia questo il luogo per una dissertazione approfondita sulle varie tecnologie di stampa 3D, forse vale la pena riassumere una classificazione di massima in base allo stato del materiale di partenza. Gli stessi materiali differiscono infatti, oltre che per composizione, anche per stato:
- le macchine FDM (Fused Deposition Modeling) partono da materiali solidi a filo (in rocchetti) che vengono portati a fusione e depositati da un ugello (come la pistola a colla calda per intenderci);
- le macchine SLA (Stereo Litographic Apparatus, e successive evoluzioni) e MJM (Multi Jet Modeling) utilizzano resine polimeriche liquide che vengono solidificate da una fonte luminosa (laser o UV) e/o di calore; la tecnologia SLA è stata la prima a venire alla luce nel 1984;
- le macchine SLS (Selective Laser Sintering, e successive evoluzioni) partono da materiali in finissima polvere che vengono sinterizzati (passaggio solido-fluido-solido) con una fonte di calore (laser o plasma); questa tecnologia è quella utilizzata per i materiali metallici.
Esistono poi tecnologie ibride che usano materiali liquidi e solidi insieme. Tra queste vale la pena ricordarne una in particolare, sviluppata dal M.I.T. di Boston, simile al SLS ma nella quale le polveri venivano unite mediante un collante spruzzato con la tecnica della stampa a getto d’inchiostro. Questa tecnologia si chiamava 3D Printing e veniva commercializzata da un’azienda (Z-Corp) successivamente acquisita negli anni ‘90 da uno dei grandi brand storici (3D Systems; l’altro è Stratasys). La cosiddetta stampa 3D era inizialmente solo una delle tante tecnologie disponibili per Rapid Prototyping, Rapid/Additive Manufacturing: successivamente, per comodità nella comunicazione di massa, è assurta, per antonomasia, a rappresentare tutte le tecnologie di creazione per accrescimento.
Con un’attenta analisi si può comprendere come le tecnologie AM debbano essere utilizzate tenendo conto di tutte le loro caratteristiche.
Adottare una tecnologia di stampa 3D richiede un completo cambio di paradigma in termini di approccio progettuale e gestionale: l’oggetto deve essere da subito pensato e progettato per essere realizzato in AM, senza gli imbuti mentali dovuti al “finora abbiamo sempre fatto così” o “quella macchina può fare quelle lavorazioni”, tenendo in considerazione altri e nuovi vincoli o limiti. Gli oggetti realizzati avranno certe caratteristiche, e non altre, in funziona del materiale, dei cicli di pre- e post-trattamento, e, per esempio, del posizionamento all’interno del volume di stampa (direzione di accrescimento). Di contro, una macchina AM può produrre letteralmente qualsiasi oggetto di qualsiasi forma, nei limiti del volume di stampa disponibile, quindi non è necessario ricollocarla o modificarla, né attrezzare una nuova linea, nel caso si voglia modificare il prodotto o fare contemporaneamente prodotti diversi. Pensiamo al forno di casa nostra: ci possiamo cucinare quello che vogliamo purché ci stia dentro. Possiamo cucinare una lasagna, subito dopo un arrosto ed il giorno dopo cuocere insieme biscotti di forme diverse.
Le tecnologie di stampa 3D/AM devono essere viste come una nuova opzione, che talvolta sostituisce e talvolta si aggiunge ed integra le tecnologie tradizionali: non è la panacea per ogni mal di testa manifatturiero, ma una soluzione che può essere insufficiente, buona, ottima od eccellente a seconda dei casi e delle condizioni al contorno.
Tutte le variabili della manifattura additiva
Abbiamo visto che produrre un oggetto con tecnologia AM può essere molto più costoso rispetto alle tecnologie tradizionali come stampaggio a iniezione, termoformatura, asportazione di truciolo, forgiatura, fusione e così via. Sarebbe però opportuno inserire nell’equazione quante più possibili variabili e parametri:
- spesa per l’acquisto dei macchinari;
- spese per le opere di setup necessarie per la messa in opera dei macchinari;
- formazione degli operatori di macchina;
- formazione dei progettisti industriali;
- caratteristiche dei materiali;
- tempi e costi di approvvigionamento di materiali, semi-lavorati, componenti (es. stampi);
- prossimità o meno della supply chain;
- caratteristiche prestazionali dei pezzi finiti in funzione di materiali e tecnologia produttiva (leggerezza, affidabilità, resistenza alle sollecitazioni, alla fatica, agli agenti chimici…);
- tempi e costi di assemblaggio (un oggetto costituito da N componenti vs un oggetto monolitico, o costituito da una frazione degli N componenti);
- tempi di riallocazione macchinari per variazione o mix di produzione;
- dimensione e layout dei siti produttivi;
- spesa energetica nei siti produttivi;
- impatto ambientale (scarti di materiale, emissione e smaltimento di sostanze inquinanti);
- spese per il popolamento dei magazzini e la gestione della logistica dei ricambi.
Facciamo un esempio pratico, già ora attuale nel settore aeronautico. Diverse normative o richieste di mercato impongono ai produttori di popolare e gestire magazzini pieni di ricambi per diversi anni, al fine di consentire al cliente/consumatore di potervisi approvvigionare in caso di necessità a costi abbordabili ed in tempi rapidi.
Il costo dei meri pezzi di ricambio è una passività rilevante per il produttore perché immobilizza, per definizione, un’enorme quantità di capitali a fronte di ricavi imprevedibili. Al di là di eventuali questioni di obsolescenza programmata, su base storica è possibile prevedere quante unità di un certo pezzo di ricambio saranno necessarie in un certo lasso di tempo, ma si tratta comunque di stime che impongono di avere dei margini di sicurezza (uguale extra costi). A questo si aggiungano i costi della logistica: costruzione o affitto e gestione dei magazzini, incluso il personale, dei trasporti per alimentare il magazzino o per far giungere a destinazione il ricambio). Spesso il costo del trasporto è superiore al valore del pezzo! Quasi sempre quello che all’utilizzatore finale costa qualche decina o centinaio di euro all’azienda costa diverse migliaia, o viceversa, la somma dei costi dei singoli pezzi di ricambio è diverse volte superiore all’acquisto del macchinario completo.
Immaginiamo ora uno scenario in cui una multinazionale manifatturiera (inteso come chiunque abbia un mercato internazionale, indipendentemente dalle dimensioni aziendali specifiche) non abbia pressoché alcun magazzino distribuito, ma “solo” una serie, strategicamente allocata dal punto di vista geografico, di piccoli laboratori di produzione AM, oppure di partner certificati locali dotati di macchinari AM. Alla richiesta del pezzo di ricambio X:
- l’azienda manda l’ordine di produzione al laboratorio o partner locale;
- potrebbe addirittura mandare in stampa il pezzo da remoto (non è fantascienza, è il presente, se si vuole), senza divulgare o condividere alcun know-how;
- segnala immediatamente al cliente quando sarà pronto per il ritiro o quando gli sarà consegnato da un corriere locale.
Spesso il valore di un pezzo di ricambio non si misura su quanto costa produrlo o a quanto lo si può vendere, ma da quanto è critica la sua mancanza per chi ne ha bisogno. Un elemento del costo di pochi euro può tenere a terra un aereo per diverse settimane o bloccare un’intera linea di produzione, con danni per diversi milioni. Ipotizziamo che il costo di acquisto del ricambio sia 100 euro con la catena produttivo-logistica tradizionale e che l’azienda spenda 100 M di euro/anno per mantenerla (chiaramente per quel codice prodotto e altre centinaia o migliaia). Se il costo di produzione del ricambio prodotto in AM fosse di 1.000 o anche di 10.000 euro, ma all’azienda la catena agile in AM costasse complessivamente 10 M euro/anno, quest’ultima potrebbe comunque far pagare ancora 100 euro al cliente, facendolo felice (magari con un servizio migliore), perché risparmierebbe ben 90 M euro/anno. Senza considerare che, per sua natura, la tecnologia AM è molto sostenibile (economicamente e ambientalmente): non ci sono sprechi di materiale e quasi sempre quello che si avanza può essere reimpiegato direttamente. La prima critica a questo scenario sta nel fatto che non è possibile sostituire l’AM a tutti i processi produttivi attuali: la risposta è chiedere il motivo per cui non la si stia ancora utilizzando in tutti quegli ambiti dove sarebbe attualmente possibile, anche solo economicamente.
Come realizzare mascherine riutilizzabili
Un esempio pratico di interazione e integrazione tra tecnologia di stampa 3D e tecnologie più tradizionali lo troviamo in una serie di video caricati su YouTube a cura di un’azienda USA produttrice di materiali per stampi, Smooth-On: un tecnico mostra come creare in poche ore, in tiratura multipla, mascherine in silicone e uretano riutilizzabili (addirittura lavabili in lavastoviglie), utilizzando filtri HEPA derivati dai sacchetti per aspirapolveri (il test sulla resistenza all’autoclave per la sterilizzazione è stato superato; sulle capacità di filtraggio FPP nulla è ancora dato sapere). In questo caso viene descritto un processo già in uso presso molte aziende manifatturiere:
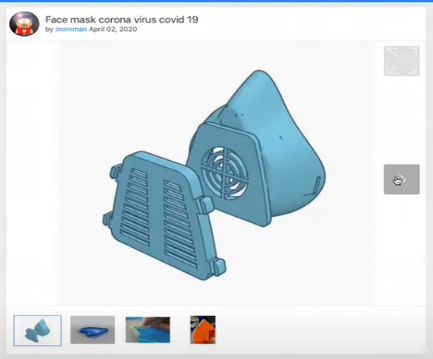
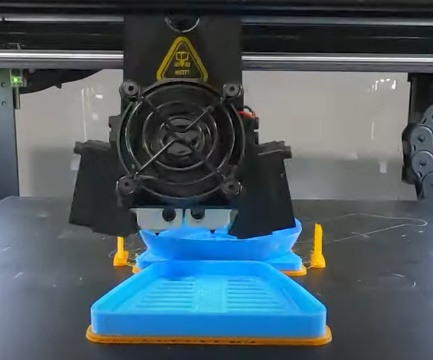
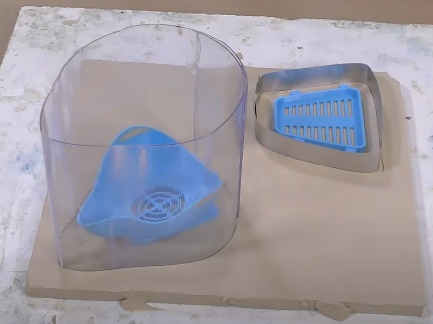
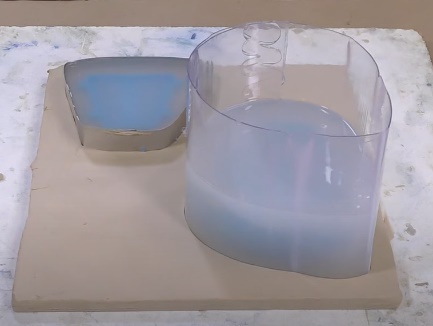
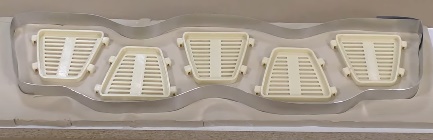
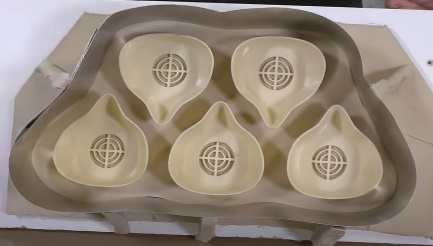
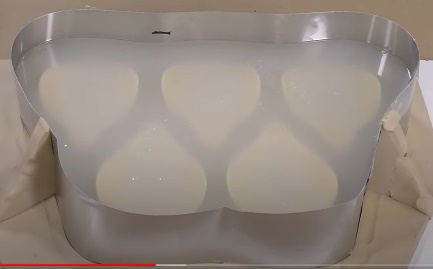
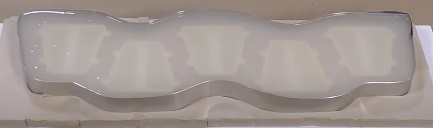
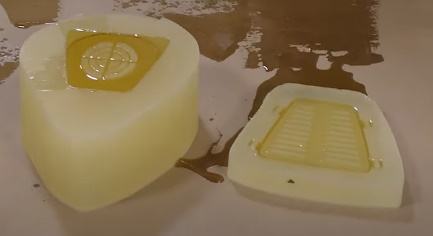
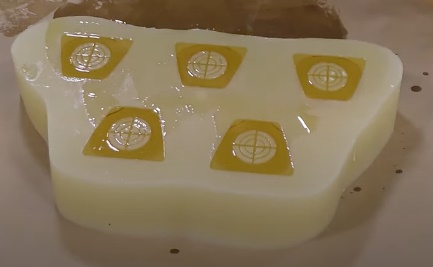
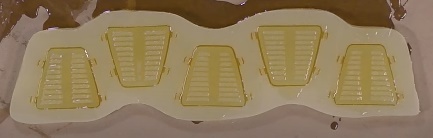
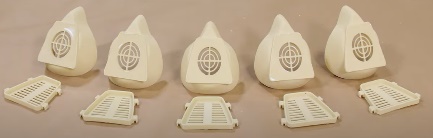

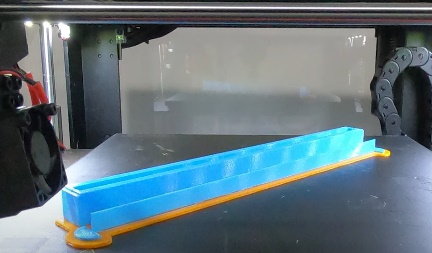
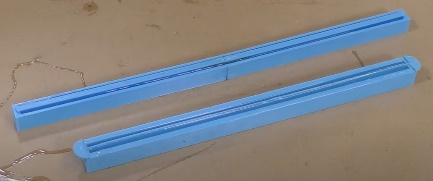
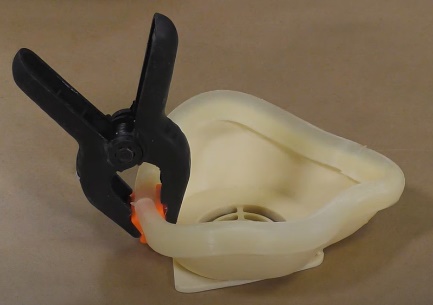
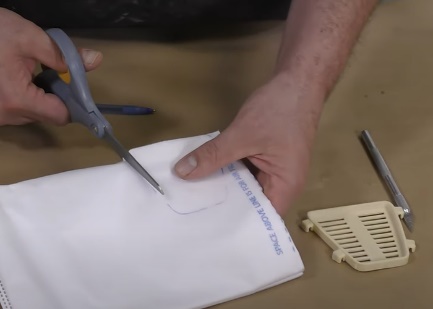
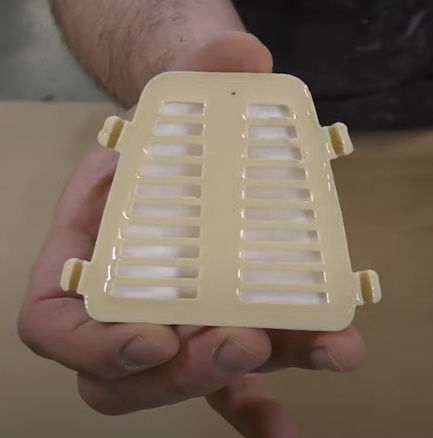
Foto 8 – Fasi della realizzazione di una mascherina con tecnologia di stampa 3D (FDM) e stampi in silicone
- l’oggetto viene modellato con CAD 3D (in questo caso i modelli di maschera, guarnizioni ed elastici sono stati scaricati gratuitamente dal sito Thingiverse);
- si crea il prototipo velocemente con una stampante 3D (FDM in questo caso);
- il prototipo viene utilizzato come calco per creare uno stampo in silicone;
- lo stampo viene utilizzato per creare l’oggetto (maschera + tappo sede filtro) in altro materiale (uretano qui) più velocemente di quanto sarebbe con la stampa 3D e con un materiale più adatto;
- con i primi componenti (mascherina completa in uretano) si creano altri stampi multipli (5x) in silicone;
- gli stampi realizzati sono utilizzati per una produzione più rapida e consistente dell’oggetto (decine o centinaia di pezzi con uno stampo in silicone, migliaia se con materiali ancor più resistenti).
Per le guarnizione di tenuta da inserire sul bordo della mascherina e gli elastici per poterla indossare, dopo aver scaricato il modello 3D, la stampante FDM ha prodotto direttamente lo stampo utilizzato per creare i componenti finali.
Il risultato è una serie di mascherine che si adattano al volto garantendo tenuta, con un filtro intercambiabile, lavabili in lavastoviglie (ad alta temperatura) e comunque sterilizzabili. Il tutto ottenuto in circa una giornata di lavoro.
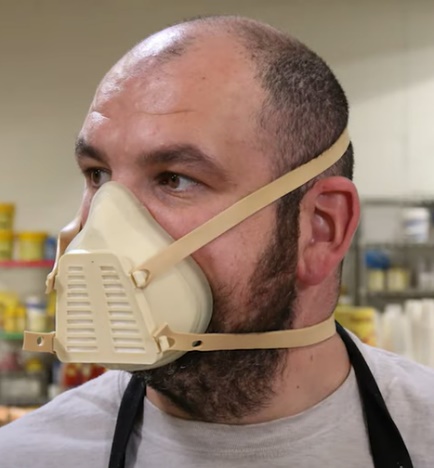
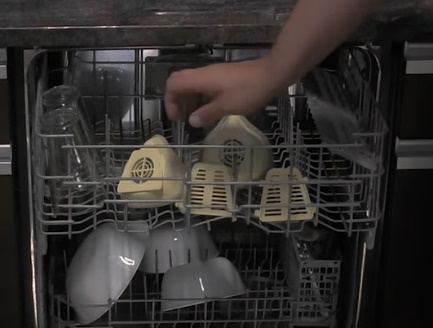
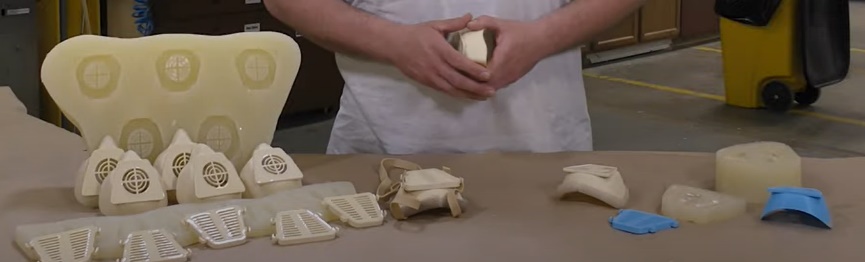
Foto 9 – La mascherina finale realizzata in uretano e silicone, con filtro. Dettagli del lavaggio in lavatrice e dei componenti realizzati nel processo.
La maggiore visibilità che la stampa 3D ha ricevuto dai media globali per il suo supporto durante l’emergenza potrebbe anche significare che le istituzioni e le imprese saranno molto più consapevoli di questa possibilità in futuro. Per esempio, alcune delle aziende produttrici di ventilatori professionali di livello medico hanno preso in considerazione l’utilizzo della stampa 3D per aumentare rapidamente le proprie capacità produttive. Dopo la crisi Covid-19 sarebbe sorprendente se la maggior parte degli ospedali non finisse per avere una stampante 3D sul posto (per un approfondimento).
Si può ipotizzare nel breve una ampia diffusione delle tecnologie di stampa 3D per far fronte a nuove, e talvolta inevitabili, interruzioni della catena di approvvigionamento, oltre che per migliorare come era già in pre-Covid, le prestazioni tecniche ed economiche di un oggetto o di un macchinario.
Così come la crisi Covid-19 ci ha mostrato che lo smart working è possibile su grandi numeri, se ci si attrezza e per chi può farlo, così ha evidenziato in tutto il mondo i vantaggi della stampa 3D: la crisi ha manifestato la necessità di una produzione più sostenibile (per le persone, per l’ambiente, per le imprese), con una filiera più vicina, reattiva e condivisa.
https://www.linkedin.com/in/paolomagni/