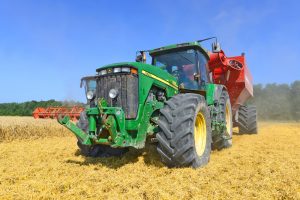
L’industria manifatturiera si è trasformata negli ultimi anni. La produzione in serie ha lasciato il posto a nuove forme di prototipizzazione “su richiesta” e alla manifattura personalizzata di piccoli lotti o singoli pezzi. Questo è particolarmente vero per John Deere, colosso internazionale della produzione di macchinari e mezzi agricoli. I sistemi e i processi delle moderne aziende manifatturiere devono essere flessibili a sufficienza per adattare le linee produttive a una varietà sempre più ampia di prodotti e l’azienda tedesca ha fatto della personalizzazione dei propri prodotti un vantaggio competitivo spendibile sui mercati internazionali. Ma questo aumenta a dismisura i livelli di complessità gestionale delle fabbriche John Deere nel mondo. Negli ultimi decenni, l’applicazione dei principi del lean manufacturing – che prevedono la ricerca del miglioramento continuo, la focalizzazione sulle attività “core” e la gestione ottimizzata dei flussi di materiale – hanno aiutato l’azienda a ridurre sprechi e inefficienze ma si è trattato di un approccio tattico più che di un orientamento di lungo termine. Una strategia di produzione che, invece, si è concretizzata grazie ai progressi ottenuti sul fronte IoT, Industria 4.0, cloud, Big Data e AI (intelligenza artificiale). Il progetto pilota della smart factory John Deere di Mannheim (Germania) è stato realizzato per sfruttare al massimo le sinergie tra i principi propri della lean production e quelli dell’Industria 4.0 – gestione efficiente ed efficace dei flussi informativi, eliminazione delle ridondanze a livello di gestione dei dati, processi self-controlled e decentralizzati.
Indice degli argomenti
Il magazzino si auto-gestisce
L’architettura applicativa si fonda sulla piattaforma d’integrazione IBM Bluemix e impiega tecnologie di
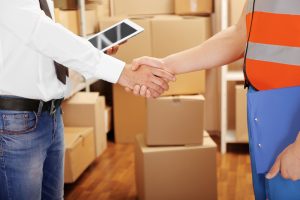
identificazione in radiofrequenza (Rfid) degli ordini, raccolta ed elaborazione dei dati provenienti dai sensori (tramite tag Rfid) e sistemi di assistenza ai lavoratori della fabbrica intelligente basati sulle funzionalità cognitive di IBM Cognos.
La soluzione sviluppata abilita la gestione intelligente e autonoma degli ordini dei componenti, sulla base dell’identificazione automatica degli stessi, la consegna immediata dei dati dell’ordine al sistema pick-to-light e la gestione automatizzata dei feedback da parte dello stesso sistema. Il pick-to-light è utilizzato nei casi in cui l’alta velocità di prelievo e la bassa percentuale di errore sono fattori chiave. Un sistema di luci facilmente visibili, collocate direttamente sullo slot di stoccaggio, indica dove prelevare l’articolo e un display segnala l’esatta quantità da prelevare. Tutte le informazioni sono scambiate in tempo reale con il sistema generale di gestione dei materiali e del magazzino. A completamento della soluzione di gestione del magazzino anche un’App (TellMeWhatsHappening@TheLine), che permette di identificare velocemente eventuali anomalie. L’App integra un sistema di riconoscimento del linguaggio naturale che permette di gestire in modo facile e rapido i problemi, permettendo di fatto un’accelerazione dei tempi d’intervento e manutenzione.
La manutenzione? Più facile con il passo-a-passo su tablet
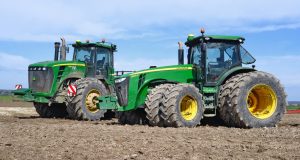
Le procedure di manutenzione all’interno degli impianti di John Deere, votati a una produzione volutamente complessa ed estremamente personalizzata, possono essere particolarmente complicate. Può essere, infatti, difficile per le squadre di tecnici compiere la diagnosi del problema e trovare la giusta soluzione, specie se il manutentore si deve destreggiare tra diversi manuali operativi. L’obiettivo del progetto era di dotare i tecnici di strumenti di accesso in tempo reale alle informazioni giuste, quelle che permettono di identificare con facilità il problema e suggeriscono la soluzione adatta. Con il tablet in dotazione, infatti, i manutentori possono scattare una foto del macchinario guasto (che diventa un dato destrutturato immesso nel sistema). Le funzionalità cognitive del sistema permettono di identificare il malfunzionamento. Sul display del palmare apparirà, quindi, l’indicazione passo a passo dell’intervento da eseguire. Il sistema è pensato per essere utilizzato senza dover digitare nulla e infatti integra la tecnologia di traduzione dal linguaggio naturale (speech-to-text e text-to-speech) per dialogare con il sistema.
Inizialmente implementata nella fabbrica storica di John Deere, a Mannheim (Germania), oggi i vertici della società hanno in programma di estendere il progetto di smart manufacturing alle 60 facility dislocate nei 5 continenti.
10 Gennaio 2017
IBM: a Monaco di Baviera si realizza l’integrazione di cognitive computing, IoT e Blockchain
Con Watson IoT IBM il Cognitive per l’Internet of Things sono già una realtà
IBM: 200 milioni di investimenti per Watson IoT e nuovi sviluppi per la Blockchain
Accordo ISS e IBM: con Watson IoT cambia il Facility Management
Immagini fornite da Shutterstock