Per le imprese che stanno valutando le opportunità dell’Industria 4.0 il primo grande obiettivo è quello di disegnare una roadmap, un percorso di sviluppo verso la digitalizzazione dei processi produttivi e di supply chain che sia coerente con la propria storia e con il proprio modello di business ma che permetta nello stesso tempo di sperimentare e individuare nuove linee di sviluppo. In questo senso appare fondamentale lavorare sulla conoscenza, sui mercato d riferimento, sui clienti e sui partner e sulle esperienze e visioni di altre imprese. Per EY il grande tema della conoscenza rappresenta il vero asset per affrontare un percorso Industria 4.0 e proprio per questo ha sviluppato incontri e workshop finalizzati a costruire uno specifico valore di conoscenza e di condivisione sui temi della trasformazione digitale finalizzata all’Industry 4.0.
EY: ambiti applicativi e roadmap per l’industria 4.0 in Italia
Come affrontare la trasformazione digitale nelle imprese produttive e come indirizzare e costruire progetti di Industry 4.0 nelle esperienze e nelle opinioni di una serie di imprese di eccellenza
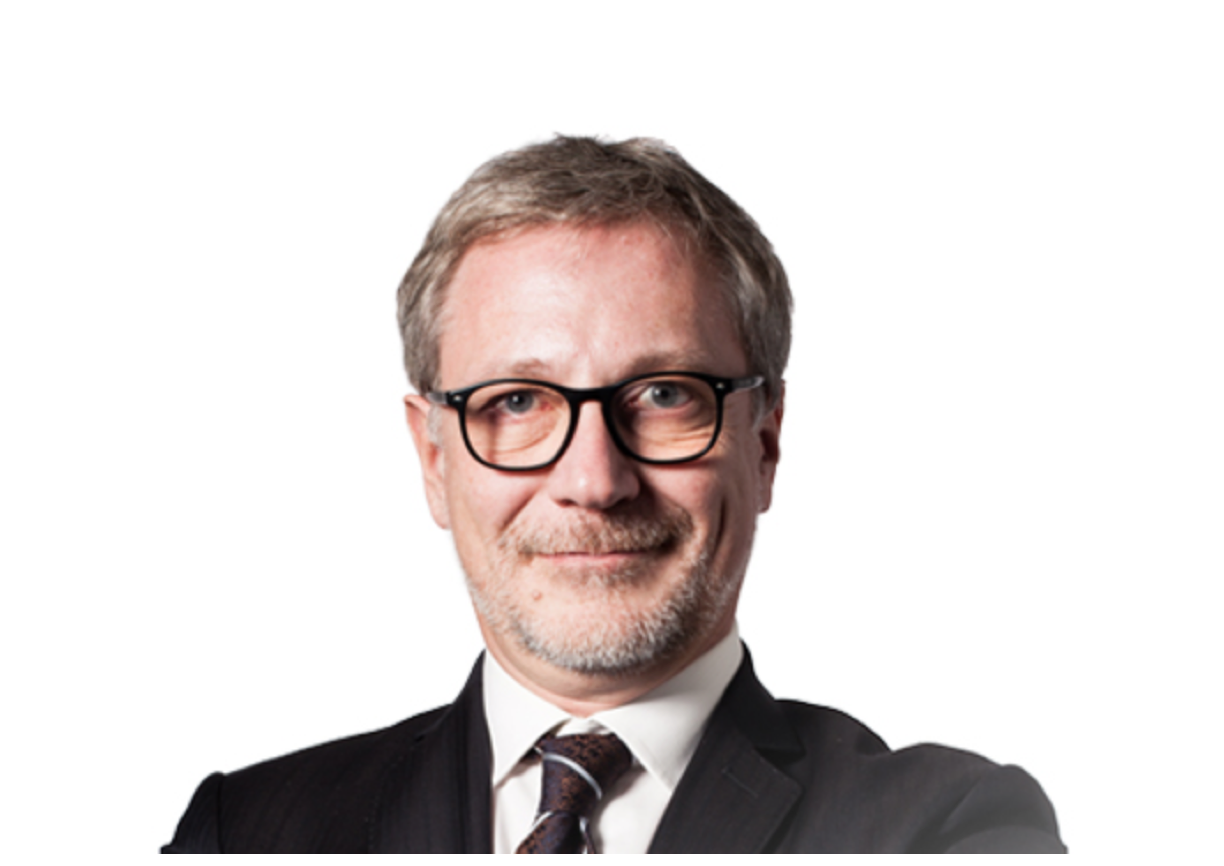
Continua a leggere questo articolo
Aziende
Argomenti
Canali
Speciale Digital Awards e CIOsumm.it