Triangle Package Machinery è un’azienda americana con sede a Chicago, specializzata nella produzione di macchinari per l’imballaggio e la sanificazione alimentare. Creata nel 1923, fin dalla sua nascita, è stata ed è un’azienda a conduzione familiare guidata, oggi, dalla terza generazione.
Per decenni gli Stati del Midwest hanno simboleggiato il cuore dell’industria manifatturiera statunitense e sono diventati espressione di quella identità americana più tradizionale e meno facile al cambiamento. L’Illinois, in particolare, è stato a lungo il crocevia tra l’east coast e la California: luoghi verso i quali molte realtà industriali e manifatturiere sono migrate per cercare di espandere la propria produzione e ingrandirsi.
Triangle Package, al contrario, ha mantenuto la struttura originale riuscendo allo stesso tempo ad aumentare produzione e clienti in molti altri Stati senza la necessità di abbandonare la città di origine.
Ha intrapreso un percorso di modernizzazione nell’intero processo di lavoro re-investendo in risorse e tecnologie, ma anche nella ricerca e nelle competenze con la precisa volontà di rinnovare la forza lavoro. Ha rivoluzionato le modalità di produzione individuando, allo stesso tempo, nuovi prodotti e nuove esigenze per soddisfare prima di ogni cosa, i clienti.
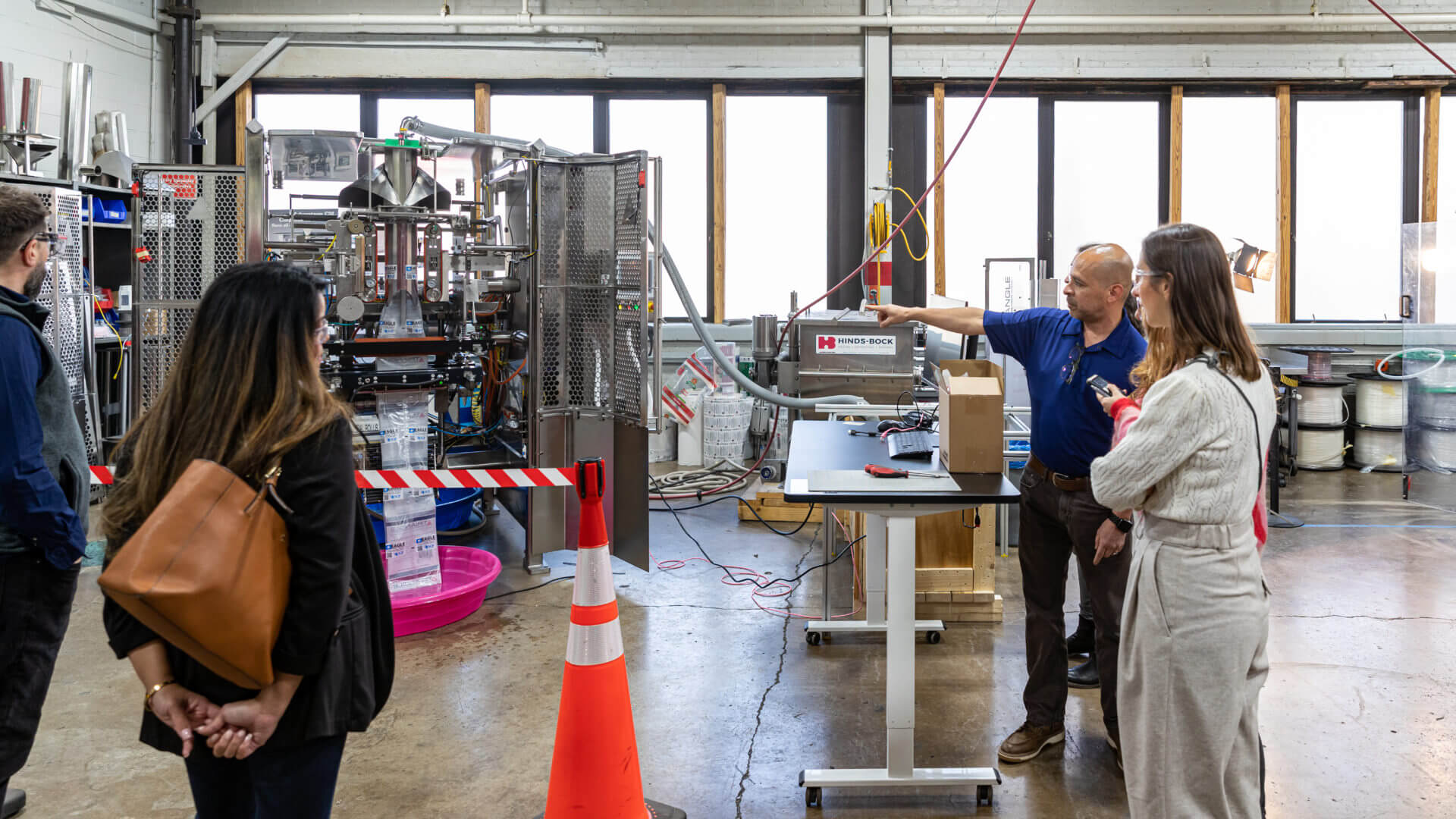
Negli anni, inoltre, ha anche coltivato una strategia di collaborazione inserendo nei propri macchinari componenti Rockwell Automation fino a diventarne un partner OEM Gold, con lo scopo di essere accompagnato nella ricerca di soluzioni nuove da implementare.
Indice degli argomenti
La stessa sede, ma completamente modernizzata
Per raggiungere l’azienda si percorre Diversey Parkway, una tra le principali strade del north side di Chicago che divide i quartieri più popolari e anche più complessi, della città fino a raggiungere i sobborghi occidentali. Oggi, Triangle Package ha un impianto di produzione di 120.000 piedi quadrati (circa 11.000 mila metri quadri) e 190 dipendenti, la maggior parte molto giovani.
I macchinari che realizza per gli imballaggi sono utilizzati in tutti i segmenti alimentari, dai cereali alle caramelle, ai prodotti freschi agli alimenti surgelati. Le soluzioni comprendono il confezionamento verticale VFFS (Vertical Form Fill Seal), pesatrici combinate, astucciatrici, confezionatrici e sistemi di caricamento/deposito di vassoi con soluzioni che garantiscono cambi rapidi tra formati e dimensioni diverse di packaging come spiega Luis Torres, Director, Product Line Management di Triangle.
Oggi, in azienda tutto parte dalla ricerca e sviluppo su cui Triangle reinveste gran parte dei profitti annuali. “Abbiamo indirizzato la ricerca e sviluppo verso soluzioni che vadano ad intercettare le esigenze del cliente e siano spendibili sul mercato” ha spiegato N’Gai Merrill, Chief Operating Officer dell’azienda. Ad esempio, sono state create astucciatrici con il cambio formato automatico per permettere ad un produttore di cereali di semplificare le operazioni, facilitare i propri operatori e risolvere problemi legati alla carenza stessa della manodopera.
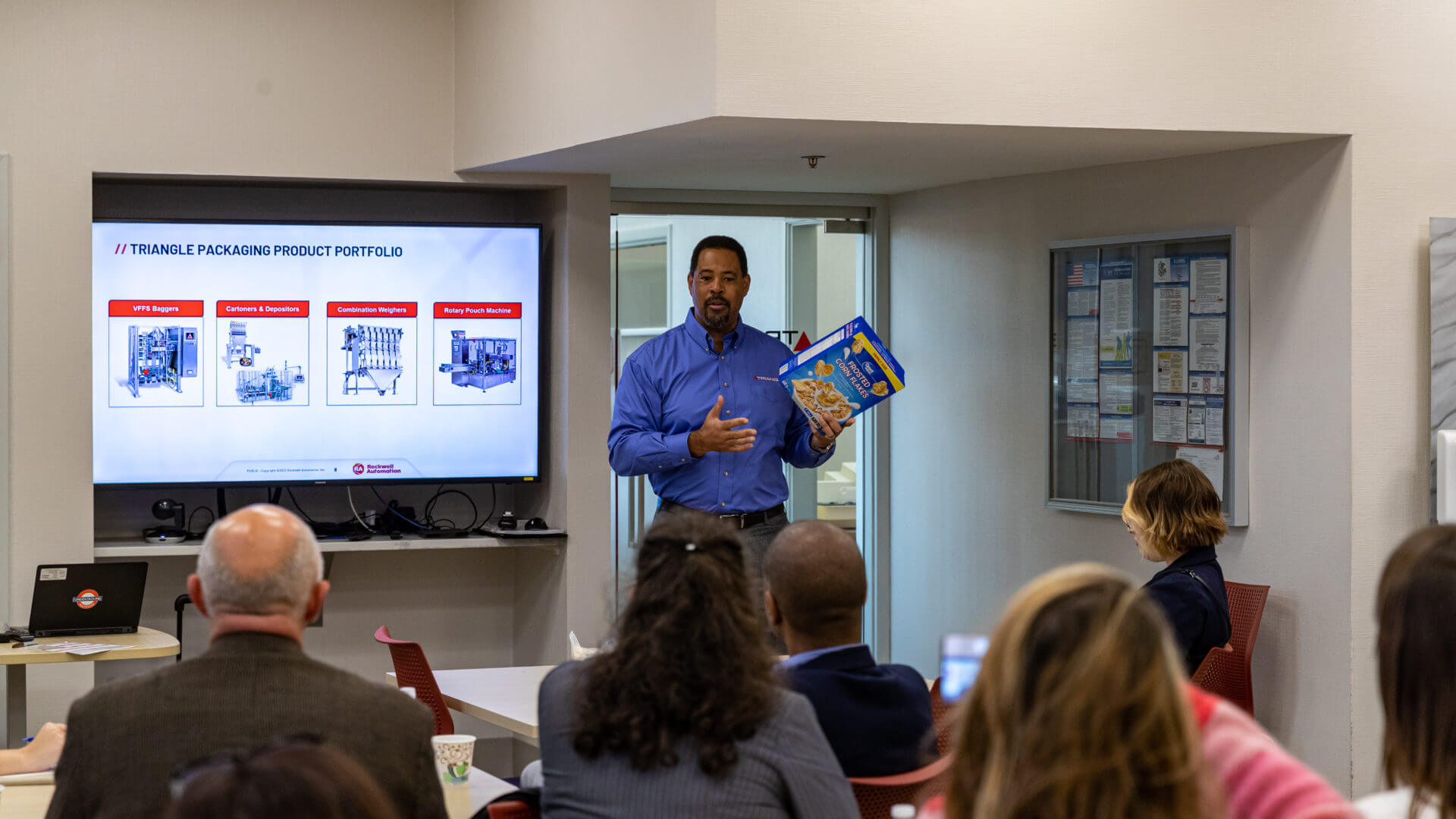
Allo stesso tempo, sono stati introdotti protocolli IO-Link all’interno delle macchine VFFS per separare alcuni componenti fuori dalla scatola di controllo riducendo al minimo lo spazio di ingombro della macchina e del cablaggio e soddisfare esigenze di progettazione e sanificazione sanitaria.
Semplificare e personalizzare la produzione: lean manufacturing
Ogni parte viene progettata e realizzata all’interno dello stabilimento di Chicago. Da qui, una volta assemblati e poi testati, i macchinari vengono spediti ovunque ci sia una richiesta.
La produzione dei singoli componenti che vanno a completare ogni macchinario non avviene per lotti o su ipotesi di vendita ma è indirizzata al progetto di un determinato macchinario già contrattualizzato.
Questo permette all’azienda di lavorare su ordinazione, massimizzare i tempi controllando ogni singolo slot di realizzazione e soprattutto di ridurre lo spazio fisico del magazzino.
Le materie prime, come le lastre in acciaio, vengono ordinate quando necessitano e sono disponibili nel giro di pochi giorni. Ogni singola fase di lavorazione viene monitorata in tempo reale per creare sinergie, continuità ed individuare eventuali rallentamenti o colli di bottiglia utilizzando una soluzione ERP di ultima generazione.
Personale qualificato, automazione e distribuzione degli spazi
L’ottimizzazione degli spazi unita alla capacità di mantenere l’intera produzione nello stesso stabilimento è stato uno degli obiettivi su cui il gruppo Triangle ha deciso di investire. L’azienda ha sfruttato nuove pratiche di automazione per ottimizzare e aumentare la capacità produttiva. Sono state eliminate sia le attrezzature che le tecnologie legacy ed introdotte soluzioni di lavorazione avanzate come gli utensili ad alta velocità.
Sono state testate diverse soluzioni per semplificare le operazioni di saldatura grazie a personale specializzato e alle forti sinergie tra competenze ingegneristiche ed esperienza; introdotti monitor per postazione di lavoro e dispositivi indossabili integrati con caschetti in grado di fornire e gestire informazioni e allo stesso tempo, permettere agli operatori di muoversi in libertà e sicurezza. Sono stati assunti sostituendo il personale andato in pensione, giovani altamente specializzati (ci sono oltre 30 ingegneri) ed inseriti in modo trasversale ai diversi reparti favorendo un forte senso di appartenenza all’azienda.
All’interno della struttura completamente aperta è sorprendente osservare l’ottimizzazione e la distribuzione degli spazi così come la capacità di personalizzazione da parte dei dipendenti. Uno stile tutto americano con un fascino anche un po’ retrò (c’è un’area dedicata ai veterani) di un’azienda che nei fatti è altamente moderna e giovane.
La sigillatura a ultrasuoni
Uno degli obiettivi dell’azienda è quello di creare macchinari sempre più orientati al cliente. Applicazioni in grado di rispondere a esigenze specifiche e basate su tecnologie che creano un vantaggio concreto per gli utilizzatori, come costi di produzione più contenuti, un minor tempo di fermo macchina e soprattutto, un risparmio energetico.
Un esempio è la sigillatura a ultrasuoni che a differenza di quella a caldo, utilizza energia solo quando è in funzione. L’azienda ha progettato e realizzato insaccatrici con ganasce a sigillatura ad ultrasuoni che trovano impiego nell’industria delle polveri e delle insalate ma possono essere utilizzate anche in altri ambiti. Un chiaro vantaggio di efficientamento energetico ancora poco utilizzato a causa dei costi e della particolare attenzione richiesta dalla manutenzione. Ma è anche una tecnologia in cui l’azienda crede molto e continua ad investire.
Un OEM in grado di implementare soluzioni innovative
Ventennale è la stretta collaborazione dell’azienda con Rockwell Automation, la multinazionale specializzata in sistemi di automazione industriale. “Oltre ad utilizzare i nostri sistemi specifici per i macchinari, c’è una forte sinergia tra team per testare nuove soluzioni. Utilizziamo la nostra tecnologia e la nostra esperienza nel settore per raggiungere risultati sostenibili, per ridurre i consumi energetici fino a risparmiare sui costi” ha spiegato Niki Lococo, OEM Account Manager di Rockwell.
Ultimamente, il team di Rockwell Automation ha collaborato con gli ingegneri di Triangle per ottimizzare le operazioni dei macchinari attraverso una soluzione a cavo singolo e ridurre al minimo la corrente richiesta per azionare il motore e ottenere, così un risparmio. Tra gli obiettivi anche quello di eliminare la differenza termica nel passaggio richiesto per l’implementazione tra due classi di azionamenti Kinetix dopo aver riscontrato alcuni problemi.